Router spiral cutting bit question
microxl
16 years ago
Related Stories
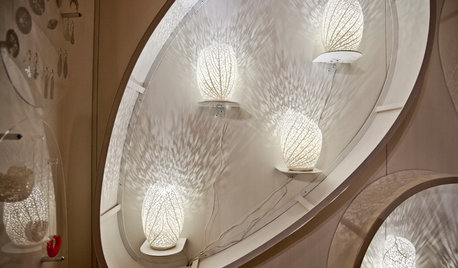
TASTEMAKERS3D Printing Takes Furnishings to New Heights at ICFF 2013
See how three-dimensional printing, laser cutting and other innovative technologies are changing the face of furnishings
Full Story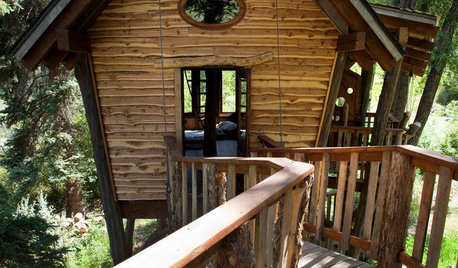
TREE HOUSESTour a Fantastical Tree House for Kids and Adults Too
For an architect and a master woodworker, a magical tree house answers the question, ‘What would you do if you could do anything?’
Full Story
INSIDE HOUZZHouzz Prizewinners Take Their Kitchen From ‘Atrocious’ to ‘Wow’
A North Carolina family gets the kitchen they always wanted — and not a minute too soon — courtesy of the Houzz sweepstakes
Full Story
REMODELING GUIDES10 Tips for Choosing and Working With a Builder
Make your construction experience a happy one by following these steps
Full Story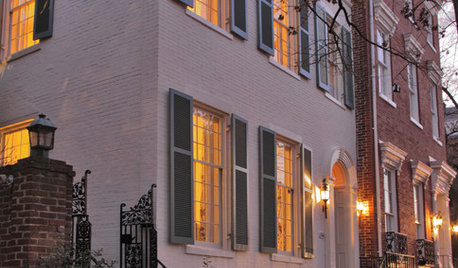
REMODELING GUIDESShould You Remodel or Just Move?
If you're waffling whether 'tis better to work with what you've got or start fresh somewhere else, this architect's insight can help
Full Story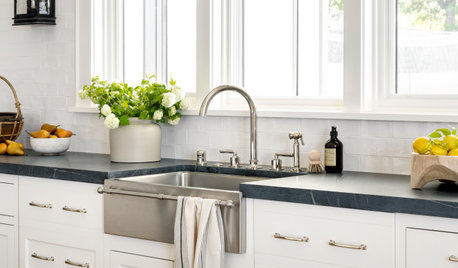
KITCHEN DESIGN8 Kitchen Sink Materials to Consider
Learn the pros and cons of these common choices for kitchen sinks
Full Story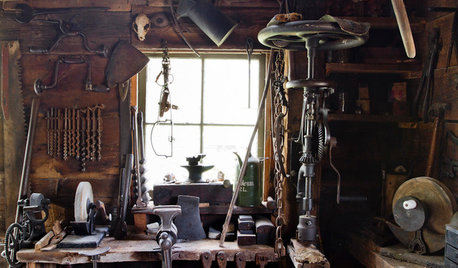
MATERIALSAre You a Maker? Show Us Your Favorite Tool or Material
Houzz Call: A tool or material can be a maker’s best friend. We’d like to see your favorite — and what it helps you achieve
Full Story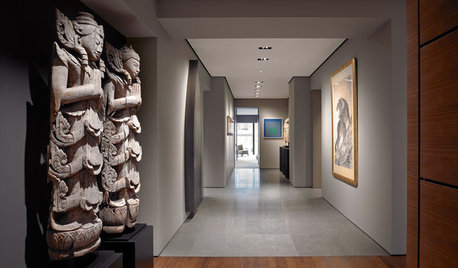
DESIGN DETAILSDesign Workshop: The Modern Wall Base, 4 Ways
Do you really need baseboards? Contemporary design provides minimalist alternatives to the common intersection of floor and wall
Full Story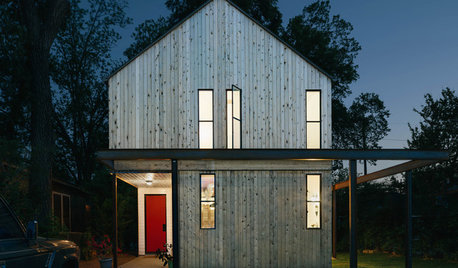
MOST POPULARHouzz Tour: Elbow Grease and Steel Create a Modern Texas Farmhouse
Talk about DIY. This couple acted as architect, interior designer and general contractor to build a one-of-a-kind home on a budget
Full Story
kmealy
User
Related Professionals
Hammond Cabinets & Cabinetry · New Castle Cabinets & Cabinetry · North Bay Shore Cabinets & Cabinetry · Channahon Carpenters · Alexandria Flooring Contractors · Cincinnati Flooring Contractors · Edmonds Flooring Contractors · Lakeville Flooring Contractors · Mount Vernon Flooring Contractors · Powder Springs Flooring Contractors · Chambersburg Furniture & Accessories · Lorton Furniture & Accessories · Queens Furniture & Accessories · Washington Furniture & Accessories · Fort Carson Furniture & AccessoriesmicroxlOriginal Author
User
brickeyee
kmealy
microxlOriginal Author
User
microxlOriginal Author
brickeyee
microxlOriginal Author