is plywood as economical as board lumber?
talley_sue_nyc
10 years ago
Related Stories
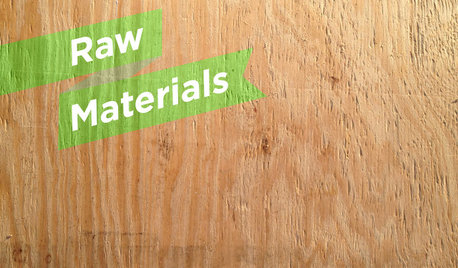
WOODThe Power of Plywood All Around the House
Of course you've heard of it, but you might not know all the uses and benefits of this workhorse building material
Full Story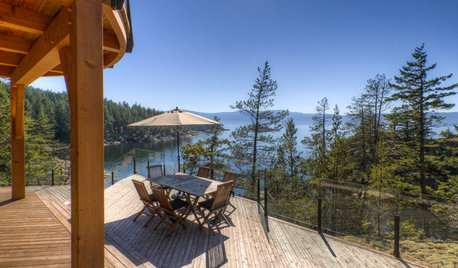
DECKSDecking Materials Beyond Basic Lumber
Learn about softwoods, tropical hardwoods, composites and more for decks, including pros, cons and costs
Full Story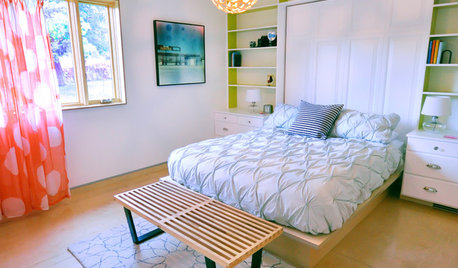
WOODTry DIY Plywood Flooring for High Gloss, Low Cost
Yup, you heard right. Laid down and shined up, plywood can run with the big flooring boys at an affordable price
Full Story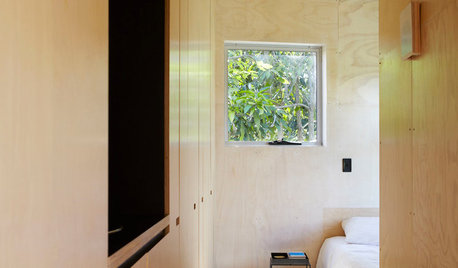
WOODDesign Workshop: Plywood as Finish
Trendproof your interior with this sensible guide to using this utilitarian material indoors
Full Story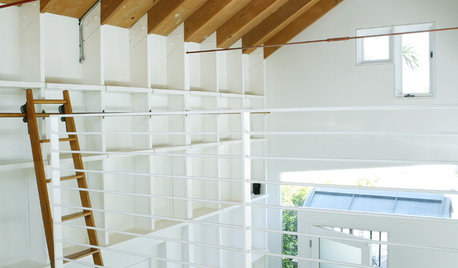

CHRISTMASBuild a Refreshingly Alternative Plywood Christmas Tree
Let others have their traditional pine. This wooden version you make yourself celebrates modern DIY style
Full Story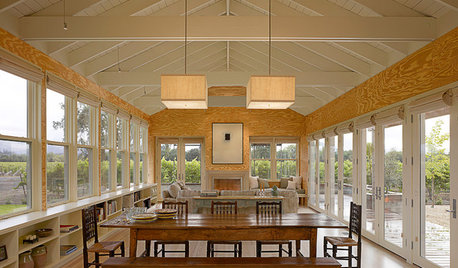
ARCHITECTUREDesign Workshop: The Beauty of Humble Materials
Discover the appeal of budget-friendly plywood, concrete and other modest surfaces
Full Story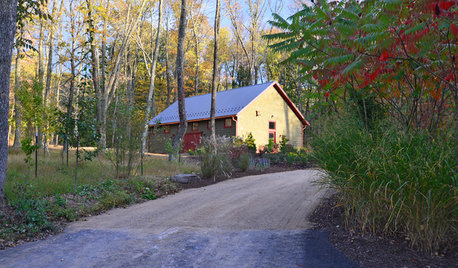
BACKYARD STUDIOSMaster Builder Crafts a Dream Workshop
A design-build firm owner uses an economical building method for his large shed and finishes it off nicely to blend into the scenery
Full Story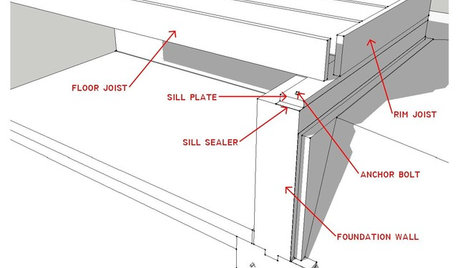
KNOW YOUR HOUSEKnow Your House: What Makes Up a Floor Structure
Avoid cracks, squeaks and defects in your home's flooring by understanding the components — diagrams included
Full Story
klem1
mike_kaiser_gw
Related Professionals
Canton Cabinets & Cabinetry · Sunrise Manor Cabinets & Cabinetry · Town 'n' Country Cabinets & Cabinetry · Saint James Cabinets & Cabinetry · Arnold Carpenters · Norfolk Carpenters · Summerlin Carpenters · Livonia Flooring Contractors · Parma Heights Flooring Contractors · Sacramento Flooring Contractors · Stoneham Flooring Contractors · Camarillo Furniture & Accessories · Huntersville Furniture & Accessories · San Diego Furniture & Accessories · Glenview Furniture & Accessoriestalley_sue_nycOriginal Author
bobismyuncle
klem1
talley_sue_nycOriginal Author
talley_sue_nycOriginal Author
klem1
talley_sue_nycOriginal Author
aidan_m
talley_sue_nycOriginal Author
aidan_m
talley_sue_nycOriginal Author
talley_sue_nycOriginal Author
talley_sue_nycOriginal Author
webfeet
talley_sue_nycOriginal Author