What's the deal-e-o? Ice & condensation on interior of windows
tulips
17 years ago
Related Stories
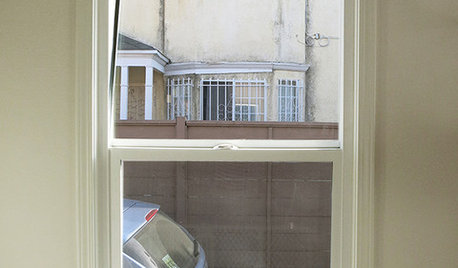
WINDOW TREATMENTS6 Ways to Deal With a Bad View Out the Window
You can come out from behind the closed curtains now. These strategies let in the light while blocking the ugly
Full Story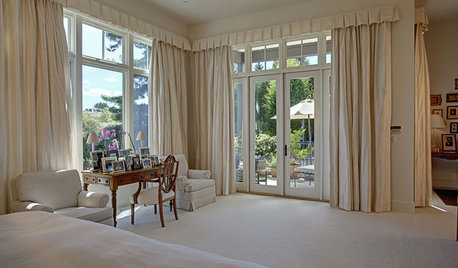
WINDOW TREATMENTSHow Low Should Your Drapes Go?
Hover, brush the floor or pool like Scarlett O'Hara's tears — we give you the lowdown on curtain length options
Full Story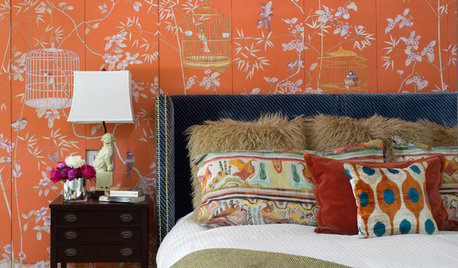
WORKING WITH PROS8 Things Interior Designers Want You to Know
Get the scoop on certifications, project scope, working from afar and more
Full Story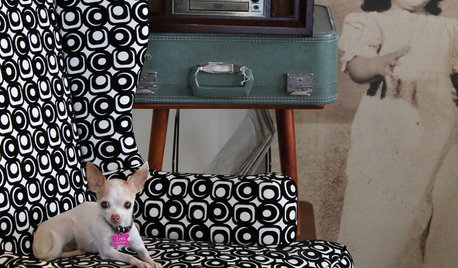
PETSWhat Chihuahuas Can Teach Us About Interior Design
Who knew these tiny dogs could be such a huge fount of design tips? Houzzers did
Full Story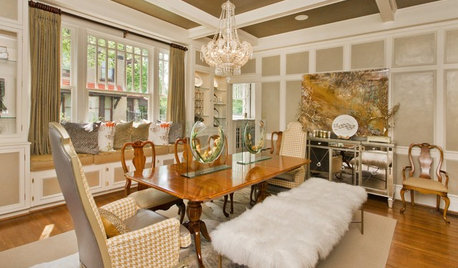
WORKING WITH AN INTERIOR DESIGNER5 Qualities of a Happy Designer-Client Relationship
Cultivate trust, flexibility and more during a design project, and it could be the beginning of a beautiful alliance
Full Story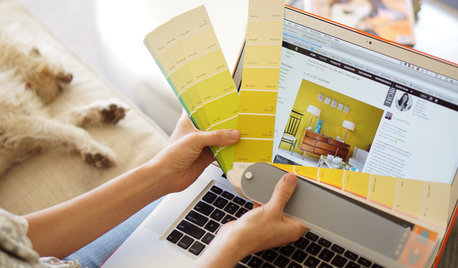
WORKING WITH PROSWorking With Pros: When You Just Need a Little Design Guidance
Save money with a design consultation for the big picture or specific details
Full Story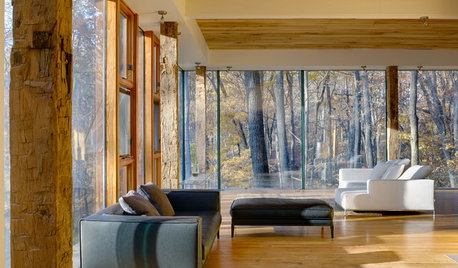
ARCHITECTUREModern or Contemporary Architecture? The Interiors Edition
See how one expert distinguishes between two popular camps of interior architecture. Do you agree with his choices?
Full Story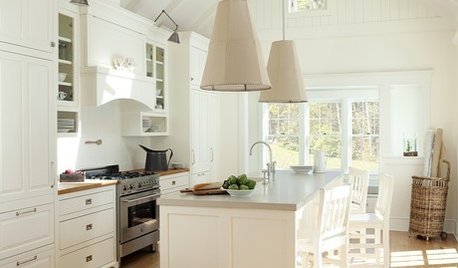
HEALTHY HOMEGet Cleaner Indoor Air Without Opening a Window
Mechanical ventilation can actually be better for your home than the natural kind. Find out the whys and hows here
Full Story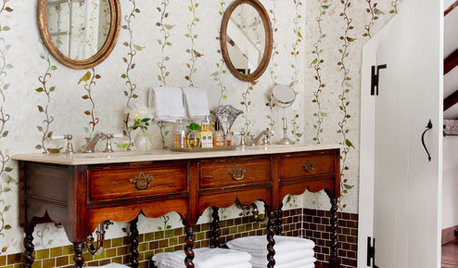
MOST POPULARYou Can Turn That Into a Bathroom Vanity?
Find inspiration in 13 unconventional bathroom vanities that are as functional as the real deal
Full Story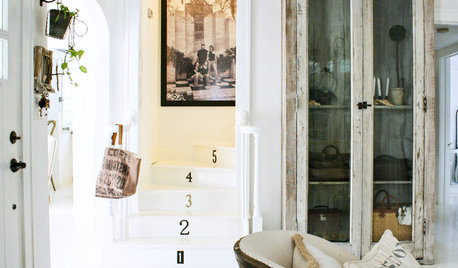
DECORATING GUIDES13 Decorating Tips for Older Homes
Preserve the personality of the past while designing for now with these tips for paint, rugs, window treatments and more
Full StoryMore Discussions
oberon476
tulipsOriginal Author
Related Professionals
Coral Gables Window Contractors · Farragut Window Contractors · Holly Hill Window Contractors · Jupiter Window Contractors · Opa Locka Window Contractors · La Habra Interior Designers & Decorators · Centereach General Contractors · Leon Valley General Contractors · Mankato General Contractors · Pinewood General Contractors · Redan General Contractors · Torrington General Contractors · Winfield General Contractors · Salisbury Carpenters · Tucson Carpentersbigfoot_2007
oberon476
oberon476
wildecatz
oberon476
wildecatz
guy_exterior_man
joan_2007
oberon476
guy_exterior_man
joan_2007
Michael
oberon476
Michael
oberon476
Michael
oberon476
bigfoot_2007
oberon476
bigfoot_2007