Cementing post footers?
gio17vani
17 years ago
Related Stories
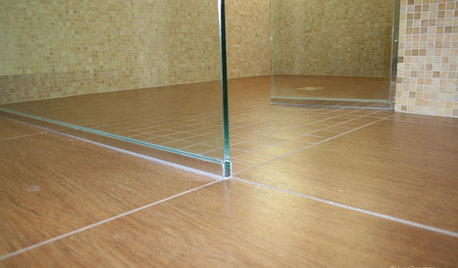
TILEEpoxy vs. Cement Grout — What's the Difference?
Grout is grout, right? Nope. Cement and epoxy versions have different appearances, durability and rules of installation
Full Story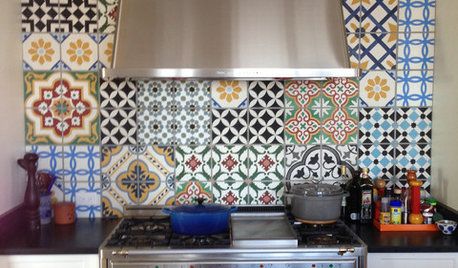
TILESo Many Reasons to Love Cement Tiles
You’ll notice their beautiful patterns right away, but cement tiles have less obvious advantages too
Full Story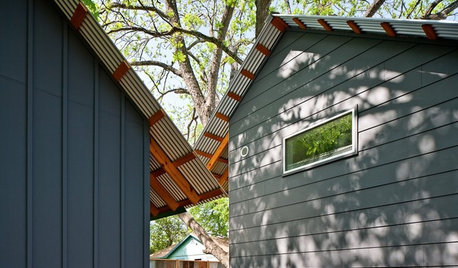
REMODELING GUIDESFiber Cement Siding Takes a Front Seat
Not just a wood or vinyl substitute, fiber cement is a stellar siding choice in its own right for modern home exteriors
Full Story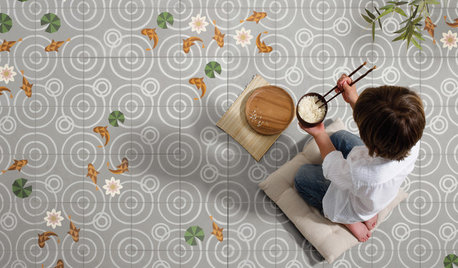
TILEWorld of Design: How Modern Geometric Designs Are Reinventing Cement
Intricate and eye-catching, the patterns of today’s cement tiles mark a break with their past while preserving an age-old technique
Full Story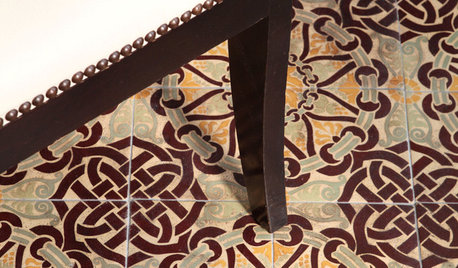
REMODELING GUIDESOld is New: Cement Tile Makes a Comeback
Get Ideas for Using Colorful Moorish-Inspired Tile at Home
Full Story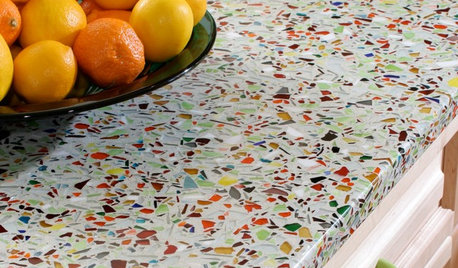
KITCHEN DESIGNKitchen Counters: Sturdy, Striking Recycled Glass With Cement
Ecofriendly and full of character, this heat- and scratch-resistant material is a great fit for custom kitchen counters
Full Story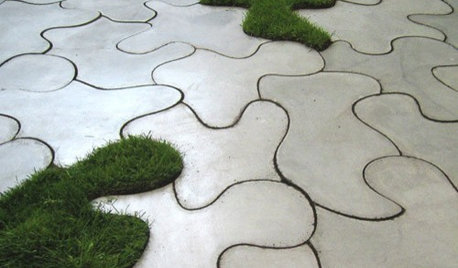
PRODUCT PICKSGuest Picks: Concrete Ideas for Patios and Decks
Look to lightweight fiber cement for functional outdoor furniture and accessories that are heavy on style
Full Story
REMODELING GUIDESYour Floor: Two Tiles to Love
Cement and quarry tiles are easy, lasting and unexpected
Full Story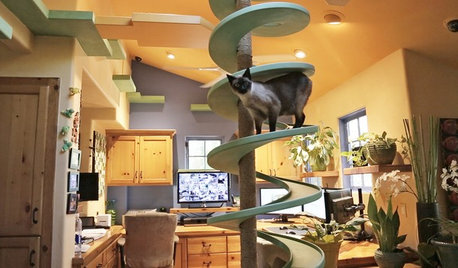
PETSWe Want to See the Most Creative Pet Spaces in the World
Houzz is seeking pet-friendly designs from around the globe. Get out your camera and post your photos now!
Full Story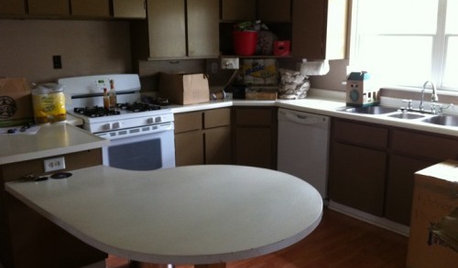
Design Dilemmas: 5 Questions for Houzzers!
Post Ideas for Landscaping for a Modern Home, Updating a Rental and More
Full Story
brickeyee
john_hyatt
Related Professionals
Atlantic City Decks, Patios & Outdoor Enclosures · Carmel Decks, Patios & Outdoor Enclosures · Foothill Farms Decks, Patios & Outdoor Enclosures · Harrisburg Decks, Patios & Outdoor Enclosures · Larkspur Decks, Patios & Outdoor Enclosures · Roseville Decks, Patios & Outdoor Enclosures · San Antonio Decks, Patios & Outdoor Enclosures · Rantoul Home Builders · Miami Home Builders · Carmel Flooring Contractors · Germantown Flooring Contractors · Saint Louis Park Flooring Contractors · South Pasadena Flooring Contractors · Suitland Flooring Contractors · Cherry Hill Siding & Exteriorsgio17vaniOriginal Author
srercrcr
nra4usa
alanchad
john_hyatt
nightrunner
srercrcr
nightrunner
philmont_2006
brickeyee
amazondk
john_hyatt
chuckr
amazondk
john_hyatt
amazondk
gio17vaniOriginal Author
chuckr
mannerstom76_yahoo_com
ken_mcdonnell