Concrete on raised deck
southtowniceman
15 years ago
Featured Answer
Sort by:Oldest
Comments (35)
deckman22
15 years agolast modified: 9 years agosouthtowniceman
15 years agolast modified: 9 years agoRelated Professionals
Fort Lee Decks, Patios & Outdoor Enclosures · Grand Rapids Decks, Patios & Outdoor Enclosures · Lenoir Decks, Patios & Outdoor Enclosures · Wyckoff Home Builders · Bethpage Flooring Contractors · Damascus Flooring Contractors · Palm Harbor Flooring Contractors · Shepherdsville Flooring Contractors · St. Louis Flooring Contractors · Beaumont Siding & Exteriors · Bountiful Siding & Exteriors · Manassas Siding & Exteriors · Oak Creek Siding & Exteriors · Riverside Siding & Exteriors · Saco Siding & Exteriorsaidan_m
15 years agolast modified: 9 years agosturgeonguy
15 years agolast modified: 9 years agosouthtowniceman
15 years agolast modified: 9 years agosturgeonguy
15 years agolast modified: 9 years agogvgemtp
15 years agolast modified: 9 years agojgmcinnis
15 years agolast modified: 9 years agoriles_j
15 years agolast modified: 9 years agohendricus
15 years agolast modified: 9 years agosouthtowniceman
15 years agolast modified: 9 years agoriles_j
15 years agolast modified: 9 years agodooer
15 years agolast modified: 9 years agosouthtowniceman
15 years agolast modified: 9 years agomikec4w
15 years agolast modified: 9 years agogardenmax-2008
15 years agolast modified: 9 years agodeckman22
15 years agolast modified: 9 years agogardenmax-2008
15 years agolast modified: 9 years agodeckman22
15 years agolast modified: 9 years agorembrandt
15 years agolast modified: 9 years agoncrealestateguy
15 years agolast modified: 9 years agojohn_hyatt
15 years agolast modified: 9 years agoncrealestateguy
15 years agolast modified: 9 years agojohn_hyatt
15 years agolast modified: 9 years agoncrealestateguy
15 years agolast modified: 9 years agosierraeast
15 years agolast modified: 9 years agocherstaf
15 years agolast modified: 9 years agojohn_hyatt
15 years agolast modified: 9 years agorembrandt
15 years agolast modified: 9 years agojohn_hyatt
15 years agolast modified: 9 years agoncrealestateguy
15 years agolast modified: 9 years agojohn_hyatt
15 years agolast modified: 9 years agocelestial
15 years agolast modified: 9 years agojohn_hyatt
15 years agolast modified: 9 years ago
Related Stories
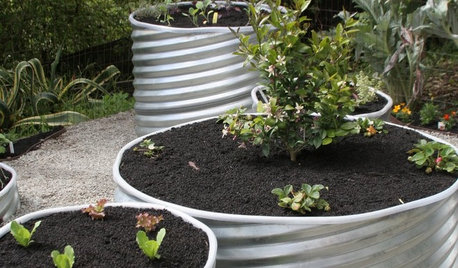
GARDENING GUIDES8 Materials for Raised Garden Beds
Get the dirt on classic and new options for raised vegetable and plant beds, to get the most from your year-round garden
Full Story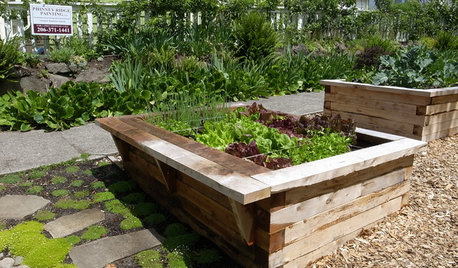
FARM YOUR YARDHow to Build a Raised Bed for Your Veggies and Plants
Whether you’re farming your parking strip or beautifying your backyard, a planting box you make yourself can come in mighty handy
Full Story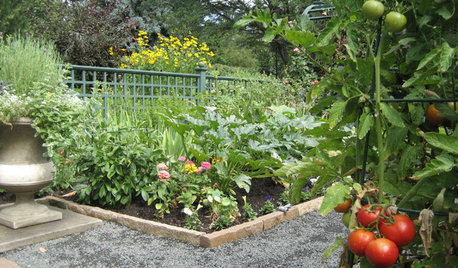
SPRING GARDENINGInspiring Raised Beds for Fall and Spring Planting
Make Your Next Vegetable Garden Even Better with Beautiful Boxes and Paths
Full Story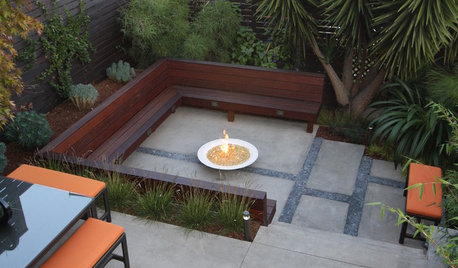
GARDENING AND LANDSCAPINGSunken and Raised Areas Take Gardens Up a Notch
Altering a landscape's grade can create energy and excitement, offering different vantage points and moods depending on the level
Full Story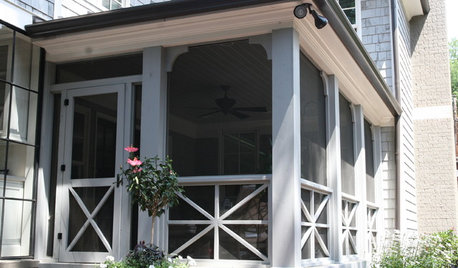
REMODELING GUIDESUnion Jack Balustrades Raise the Flag for Railing Style
Do be cross with your porch and deck railings — this intersecting balustrade design shows admirable attention to detail
Full Story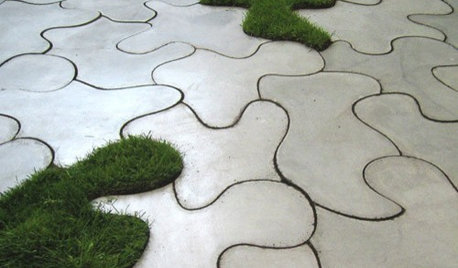
PRODUCT PICKSGuest Picks: Concrete Ideas for Patios and Decks
Look to lightweight fiber cement for functional outdoor furniture and accessories that are heavy on style
Full Story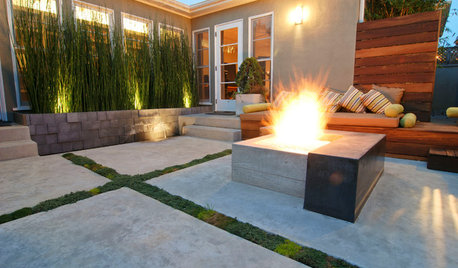
GREAT HOME PROJECTSHow to Tear Down That Concrete Patio
Clear the path for plantings or a more modern patio design by demolishing all or part of the concrete in your yard
Full Story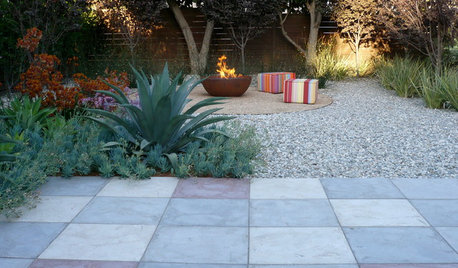
MATERIALSPrecast Concrete Pavers Make a Versatile Surface in the Garden
You can use concrete pavers in a variety of shapes and colors for your patio, walkway, driveway and more
Full Story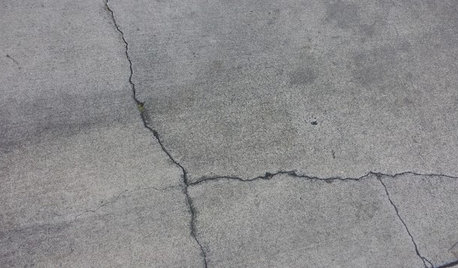
CONCRETEWhy Concrete Wants to Crack
We look at the reasons concrete has a tendency to crack — and what you can do to help control it
Full Story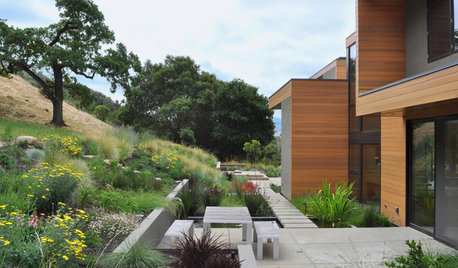
LANDSCAPE DESIGNOutdoor Style: Creative Ways With Classic Concrete
Have you cast concrete aside as being too dull or crack-prone? Learn about new design options along with the basics of using it outside
Full Story
egor_sb