My Spa Is Cracked!
ncrealestateguy
14 years ago
Related Stories
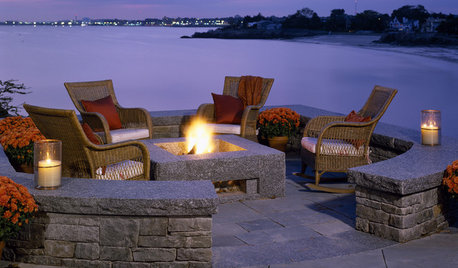
GARDENING AND LANDSCAPINGDraw a Crowd With a Fire Pit
For an alluring patio or backyard and a happy group of guests, get cracking with a fire pit
Full Story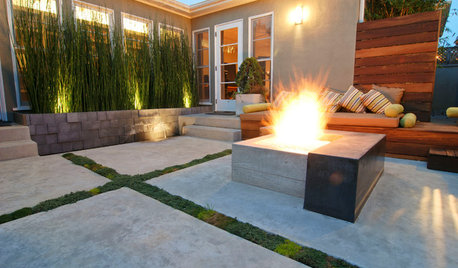
GREAT HOME PROJECTSHow to Tear Down That Concrete Patio
Clear the path for plantings or a more modern patio design by demolishing all or part of the concrete in your yard
Full Story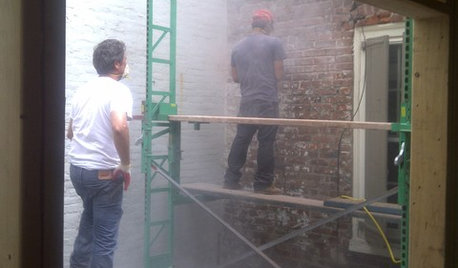
HOUSEKEEPING10 Problems Your House May Be Trying to Show You
Ignore some of these signs and you may end up with major issues. We tell you which are normal and which are cause for concern
Full Story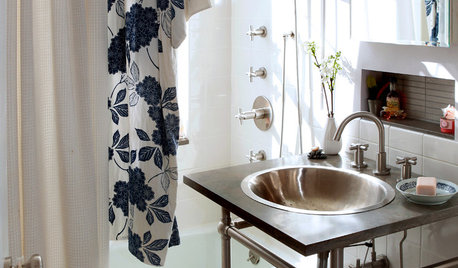
BATHROOM DESIGN8 Tiny Bathrooms With Big Personalities
Small wonders are challenging to pull off in bathroom design, but these 8 complete baths do it with as much grace as practicality
Full Story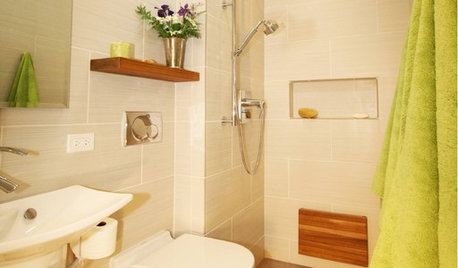
BATHROOM DESIGNMake a Tiny Bathroom Work Wonders
Light, reflection and multitasking spaces keep small bathrooms both stylish and functional
Full Story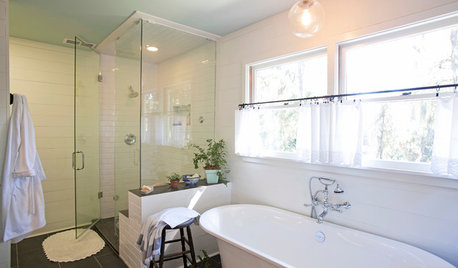
TRADITIONAL STYLERoom of the Day: Farmhouse Appeal Adds Calm and Comfort to the Bath
Country touches, natural light and a palette of simple materials make this a favorite family bath
Full Story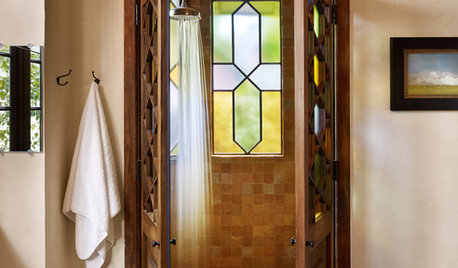
WINDOWSThe Art of the Window: 10 Ways to Elevate Your Bathroom
These window styles and treatments bring in natural light while creating a restful and rejuvenating ambience
Full Story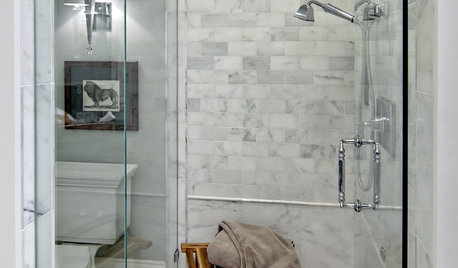
BATHROOM DESIGNHow to Settle on a Shower Bench
We help a Houzz user ask all the right questions for designing a stylish, practical and safe shower bench
Full Story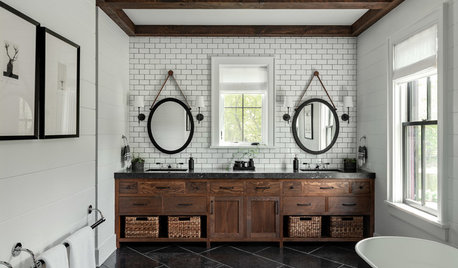
BATHROOM DESIGNBathroom Workbook: 7 Natural Stones With Enduring Beauty
Not everyone wants a marble bath. Bring organic warmth to counters, walls or floors with these hard-wearing alternatives
Full Story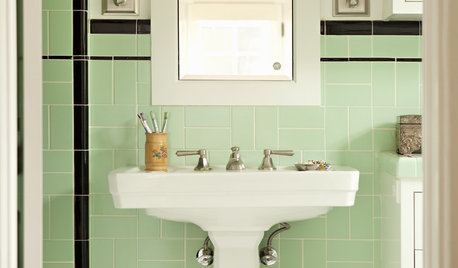
BATHROOM DESIGN9 Surprising Considerations for a Bathroom Remodel
Don't even pick up a paint chip before you take these bathroom remodel aspects into account
Full Story
ncrealestateguyOriginal Author
devildog1989
Related Professionals
Buena Park Swimming Pool Builders · Hershey Landscape Architects & Landscape Designers · Southfield Landscape Architects & Landscape Designers · Sahuarita Landscape Architects & Landscape Designers · Brentwood Landscape Contractors · Cliffside Park Landscape Contractors · College Park Landscape Contractors · North Canton Landscape Contractors · Oviedo Landscape Contractors · Shoreview Landscape Contractors · Vermilion Landscape Contractors · Woodland Landscape Contractors · Pittsburgh Decks, Patios & Outdoor Enclosures · Redmond Decks, Patios & Outdoor Enclosures · Universal City Decks, Patios & Outdoor EnclosuresncrealestateguyOriginal Author
devildog1989
loves2read
loves2read
mikethepoolguy
loves2read
golfgeek
devildog1989
mikethepoolguy
mikethepoolguy
tsunami
renovxpt
mikethepoolguy
poolguynj
renovxpt
mikethepoolguy
renovxpt
jmas65
ncrealestateguyOriginal Author
renovxpt
hv4xpy4
cascade
ncrealestateguyOriginal Author
cascade
renovxpt
conall
janetlong
loves2read
ncrealestateguyOriginal Author
renovxpt
renovxpt
cascade
loves2read
renovxpt
Dan Huber
Aqua-Link Pools and Spas
Aqua-Link Pools and Spas