Advantages of silver solder over tin/antimony?
pjb999
16 years ago
Featured Answer
Sort by:Oldest
Comments (7)
pjb999
16 years agolast modified: 9 years agoRelated Professionals
Franklin Plumbers · Forest Hill Kitchen & Bathroom Remodelers · Cocoa Beach Kitchen & Bathroom Remodelers · Green Bay Kitchen & Bathroom Remodelers · Lincoln Kitchen & Bathroom Remodelers · Martha Lake Kitchen & Bathroom Remodelers · Oxon Hill Kitchen & Bathroom Remodelers · Pasadena Kitchen & Bathroom Remodelers · Rancho Palos Verdes Kitchen & Bathroom Remodelers · Red Bank Kitchen & Bathroom Remodelers · Warren Kitchen & Bathroom Remodelers · Lawndale Kitchen & Bathroom Remodelers · Gibsonton Kitchen & Bathroom Remodelers · Plant City Kitchen & Bathroom Remodelers · Ojus Kitchen & Bath Fixturesbrickeyee
16 years agolast modified: 9 years agolazypup
16 years agolast modified: 9 years agofranktank232
16 years agolast modified: 9 years agolazypup
16 years agolast modified: 9 years agolouwatters
14 years agolast modified: 9 years ago
Related Stories
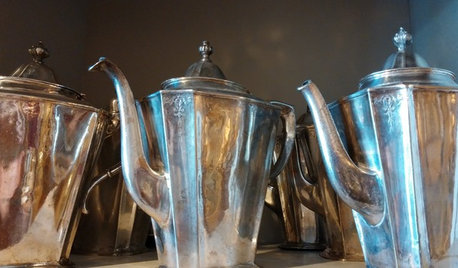
TRADITIONAL STYLEDecorating With Antiques: Silver’s Legacy
Learn how to tell sterling from plate, ways to display pieces and why silver is so darn special to begin with
Full Story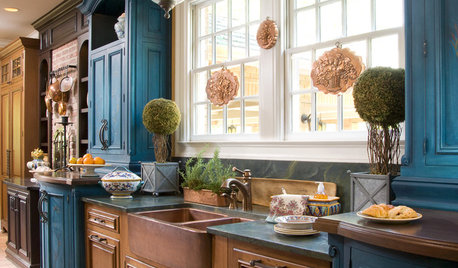
KITCHEN DESIGNKitchen Sinks: Antibacterial Copper Gives Kitchens a Gleam
If you want a classic sink material that rejects bacteria, babies your dishes and develops a patina, copper is for you
Full Story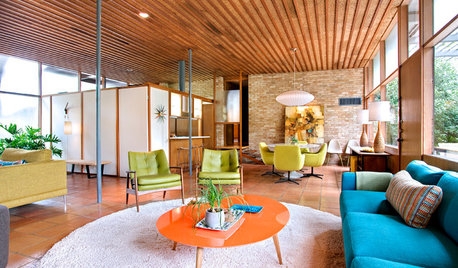
DECORATING GUIDESLook Up and Dream: 11 Ideas for an Inspired Ceiling
Think beyond the standard coat of paint, and make your ceiling pop with unexpected materials and glamorous finishes
Full Story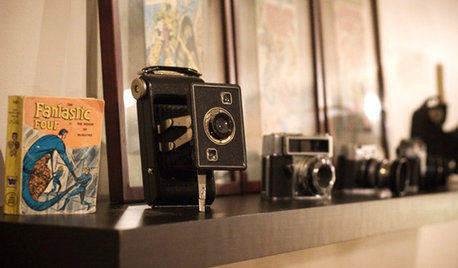
LIFEHow to Handle Inherited Things You Don’t Really Want
Whether you’ve inherited a large collection of items or a single bulky piece of furniture, it’s OK to let it go if you don’t need or want it
Full Story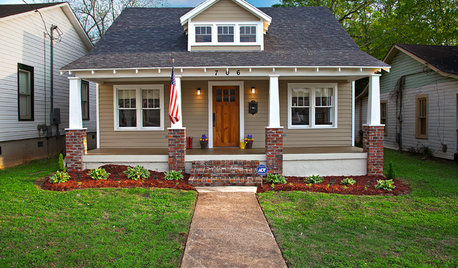
MATERIALSThe Most Popular Roofing Material is Affordable and Easy to Install
Asphalt shingles, the most widely used roof material in the U.S. are reliable and efficient, and may be right for you
Full Story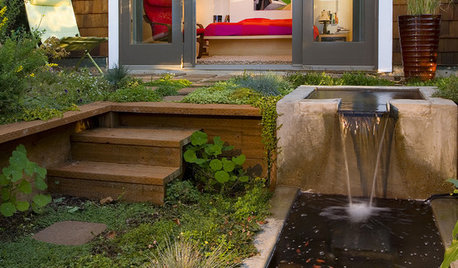
GARDENING AND LANDSCAPINGBid Bad Garden Bugs Goodbye and Usher In the Good
Give ants their marching orders and send mosquitoes moseying, while creating a garden that draws pollinators and helpful eaters
Full Story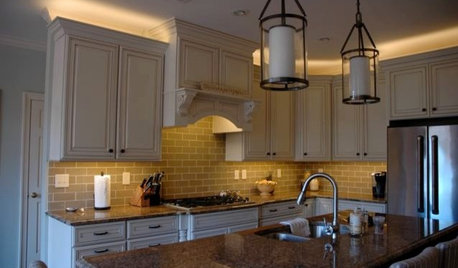
LIGHTINGThe Lowdown on High-Efficiency LED Lighting
Learn about LED tapes, ropes, pucks and more to create a flexible and energy-efficient lighting design that looks great
Full Story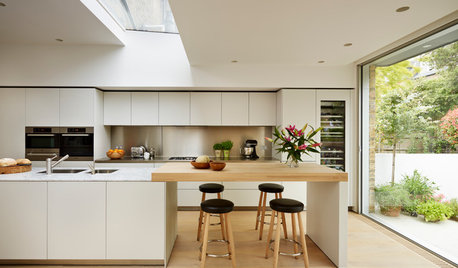
MATERIALSKitchen Ideas: How to Choose the Perfect Backsplash
Backsplashes not only protect your walls, they also add color, pattern and texture. Find out which material is right for you
Full Story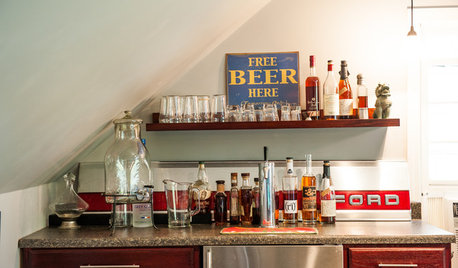
KITCHEN DESIGN15 Creative Backsplashes Full of Character
You’ll find personality aplenty in these distinctive backsplashes — and lots of inspiration too
Full Story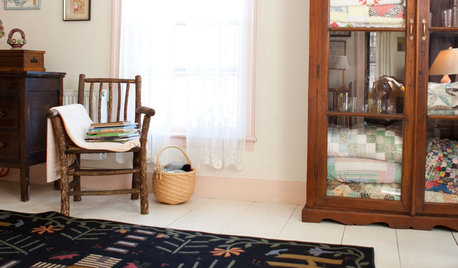
THE HARDWORKING HOMEClever Ways to Rethink the Linen Closet
The Hardworking Home: Get rid of those toppling piles with these ideas for organizing bedding, towels and more
Full StoryMore Discussions
lazypup