Another jacking up floor question
Our house is 110 years old and has two areas that need to be supported better. The kitchen area can be done with inexpensive jacks and I think we can do it ourselves. The other area is not a joist sagging problem, but more of a pier settling problem I think. It needs hydraulic lifting and a shored up pier or new pier.
I called a guy who has been moving houses for about 40 years...he looked at it and said he can do it. The thing is, he thinks it can be done quickly. I've read in several places that it should be done very gradually. I'm pretty nervous about doing it at all, much less quickly. If I want a second opinion, what sort of professional does this sort of thing? I don't think a general contractor would be my best bet.
I guess it might help if I asked the house moving guy how many inches the house needs to be raised. If it's not much, maybe it COULD be done quickly. Any cautionary advice?
Comments (28)
naominichol
18 years agolast modified: 9 years agoWe are in the exact same boat. We're in escrow with a 100 year old house, and the central post has settled and needs to be lifted and a new support put in underneath. We had a civil engineer come in and he said it needs to be jacked up about 3/4 inch when all is said and done. I have been told that even this amount needs to be done SLOWLY, as it may have taken decades to move down that much. My father is an engineer and he recommended one turn of a jack a day, so to jack it up over 5-7 days at least. This of course makes it hard to hire someone to do it. My husband and a friend feel they can jack it up and leave it until we replace the foundation in the spring, but it scares me to not have a professional in, as it is the center support post for a 2 story house. I'll be interested in what others have to say on this.
glassquilt
18 years agolast modified: 9 years agoMy dad jacked up his mom's house back in the 60's (it was about 70 years old). All the keys of the plaster broke off. As a result he had to drywall.
Related Professionals
Bethpage Kitchen & Bathroom Designers · East Peoria Kitchen & Bathroom Designers · Grafton Kitchen & Bathroom Designers · Knoxville Kitchen & Bathroom Designers · La Verne Kitchen & Bathroom Designers · Leicester Kitchen & Bathroom Designers · Mount Prospect Kitchen & Bathroom Designers · Pleasanton Kitchen & Bathroom Designers · South Barrington Kitchen & Bathroom Designers · Islip Kitchen & Bathroom Remodelers · Kendale Lakes Kitchen & Bathroom Remodelers · Red Bank Kitchen & Bathroom Remodelers · Superior Kitchen & Bathroom Remodelers · Sharonville Kitchen & Bathroom Remodelers · South Lake Tahoe Architects & Building Designerssujiwan_gw 6b MD/PA
18 years agolast modified: 9 years agoWe're going to have to raise up a corner of our kitchen wing that is sagging since the stone foundation has broken down. I did a bit of online research and the advice seems to vary with how severe the problem is (the worse it is the more you need house moving professionals) and also where, exactly, you put the lift supports attached to the jacks (like house wrighting uses the sills). Then there is the issue of multiple jacks and working in teams to effect a lift simultaneously. As mentioned--slow, REAL slow, is better and safer. I have seen 1/4 turn and 1/2 turn per week recommended. Luckily, there is no plaster in the kitchen wing, so I'm not concerned about that. Proper support for the jack is a necessity -- we have to pour a concrete footer for the jack to rest on--and making sure no wires, pipes or connectors will be affected. Most of the help sites won't come out and recommend this as a DIY activity, since it can be hazardous and cause $$$ damage if you don't know what you're doing, but they put the info out there.
brickeyee
18 years agolast modified: 9 years ago1/8 inch per week if you want to preserve plaster walls. Even then you will likely produce some new cracks.
The sag in an old joist is 'set'. When you start jacking, the entire joist moves, curve and all. The wood does not 'straighten out' to any signifiacnt degree. It has lost the little 'give' it had when new.
Jacking rate needs to account for what is moving and how the house is constructed. Fast is usually not good unless it is over a small area or does not involve walls (the sag in the middle of a room). Just be aware of the 'set' problem. Sometimes the entire curve just moves up.chaz_oh
18 years agolast modified: 9 years agoThis should get you started:
Here is a link that might be useful: Jacking up stuff
brickeyee
18 years agolast modified: 9 years agoBe very careful of the site above. It took all of about 30 seconds to find the first error:
"Common framing lumber can only handle about 625 pounds per square inch of compressive stress."
This is grossly to high, even for temporary jacking. Loads in the 50-100 PSI are often even to high for new lumber. The old stuff can often take more (it has hardened up over the years if not in a damp/high humidity location).
Metal lintels (angle iron) are the most eaily obtained pads for use when jacking, and serve to spread the load out well.
It is iften easier to place a face againstthe wood to be jacked and have the angle hang down. This allows placement centered under a joist or beam.
Another often omitted item is to keep the jack perfectly plumb. Any tipping can cause 'kick out' of the base of the jack.
A pair of lintels can be used to help spread the load on the bottom of the jack also. Typical concrete floors are only 4 inches or so thick, and not designed for the concentrated point load of heavy jacking.chaz_oh
18 years agolast modified: 9 years ago"Be very careful of the site above. It took all of about 30 seconds to find the first error:"
The article cited a footnote to the 625psi figure. Where is the evidence for your 50psi spec? Perhaps a link?
And if you had read more than 30 seconds into the article, you would have noted that the author recommends using steel plates under the jack. The whole point in mentioning the compressive strength of lumber is that bottle jacks can exceed it, therefore steel plates are needed.
Read the entire article. I see nothing wrong with his method to jack up a floor, and I've been in the business for nearly 30 years.
brickeyee
18 years agolast modified: 9 years agoI do structural design work in wooden buildings. the design limit is 50-100 PSI deoending on wood species.
Try the Wood handbook: Wood as an Enfgineering Material, Forest Products Lab, USDA.
Online for the looking.I stop reading when folks say stupid things.
nutynetie
18 years agolast modified: 9 years agoWe jacked up Mom's 3 story brick Tudor built in 1929 to replace the bearing wall & the perimeter foundation, during a complete basement remodel.
The one 'professional' we consulted gave us his opinion, (he'd done this before) we thought he was crazy and then got an engineer ($800 well spent) to come up with a plan - the building dept said ok & we were off...
Six 20 ton bottle jacks - lots of support lumber - no fancy lifter jacks - three days & we were done with the adjusting (not the concrete work).
The scariest part was the noise the house made - just like an earthquake. Lots of cracks - we didn't care about saving the plaster - nothing too severe, so we saved the plaster.
I didn't read the referenced link - maybe its a good reference / basic education to have *but only* prior to calling an engineer. Remember to ask if they carry an active Errors & Ommisions Insurance Policy !
It's such a relief when it's all said & done.
chaz_oh
18 years agolast modified: 9 years agoMost of us are or should be aware that no one should rely solely on anonymous posters in a forum as a substitute for advice from a local professional.
And unless that local professional is willing to give you his engineer's stamp on a set of plans... well, I think you get the idea.
But there is nothing wrong with gathering a consensus of information from several sources and making up one's own mind. There is rarely only 'one' correct method to do a given task. It is up to the individual to make up his/her mind which path to follow. There are many factors involved: budget, time, etc.
I don't know off the top of my head what the actual compression strength is of a particular species, say SPF (Spruce/Pine/Fir), a typical standard stud grade material. But I'll try to locate it online. If/when I do I'll repost. An actual link would have been nice.
I jacked up my 2 story '28 foursquare and replaced the sagging girder with an I-beam, and used 4 by 4s and bottle jacks for the jacking. It worked well, jacking up the entire center of the house. Don't think I wasn't nervous, but it was fine. The good thing about wood is that it will let you know if you begin to exceed its limitations. I did hire an engineer for the specs on the girder/beam/post particulars.
But before the thread is hijacked too much, realise the poster I replied to mentioned just jacking the center of a floor, and ony wanted DIY advice as a means of understanding the methods used for the project.
Quote: "info that might help if you want to consider it as a DIY job? I don't, but they will at least help me to better understand what I'm up against " End quote.
Good luck erasmus, I'm sure you'll make the right choices.
Disclaimer: Use any information gathered as a tool to further your knowlege.
chaz_oh
18 years agolast modified: 9 years agoCompression strength perpendicular to the grain:
White Fir- green- 280psi
" "- 12% moisture- 530psiE. Wht pine- green- 220psi
" "- 12% moisture- 440psiW. Wht pine- green- 190psi
" "- 12% moisture- 470psiWht spruce- green- 210psi
" "- 12% moisture- 430psiSpruce pine- green- 280psi
" "- 12% moisture- 730psiThere wasn't a listing for yellow pine, which is often the type of material used in a treated 4 by 4, but I suspect it is considerably higher than white pine.
Here is a link that might be useful: Wood Handbook -- Wood as an Engineering Material Chapter 4 page 4-7
chaz_oh
18 years agolast modified: 9 years agobrickeyee
"I do structural design work in wooden buildings."I also see you posting as an expert in the electrical forum, and have seen you posting as an expert plasterer.
Are you a design engineer, electrician, plasterer, or what?
Just curious as to who some of the 'experts' are.BreakerOff
18 years agolast modified: 9 years agoChaz,
You've been here three months.
Brickeyee has been here over three years.
Take a deep breath and settle down. These forums are civil places and we like to keep it that way. Differing opinions are certainly welcome, but personal attacks are certainly NOT. Please post in a less confrontational manner, or refrain from participating.
chaz_oh
18 years agolast modified: 9 years agoI thought I was being civil. Merely correcting and verifying information for accuracy.
Not meant to be confrontational.
By what authority do you threaten me?
brickeyee
18 years agolast modified: 9 years agoI have a good pile of engineering degrees (electrical and mechanical undergrad) and a couple masters to go with them, along with a PhD in EE. I am a registered professional engineer and have been purchasing and renovating properties for over 30 years. Top to bottom if required, but I try to avoid that since I often have to sink excessive money into the place since my subs and crews need to be paid. My labor is 'free' since I take it at the end as the owner of the property.
To smooth over the bumps in house renovations I work as an electrical engineer, and right now am working to start up a company specializing in radiation testing of semiconductors for satellite use. After less than two years we are actually doing well and have hired a couple people.
Long before the internet was a glimmer the trade information started to disappear. I learned how to repair and replace plaster walls before I even worked in a house new enough to have drywall. Along the way I even had to learn how to make run in place plaster molding (once corner of an old house had water damage to about 25 feet of molding).
Structural work came along about 20 years ago for a couple of distressed properties that had foundation issues. A have a structural PE for part time help if I need him, but few houses are complicated enough to require more then Superbeam and careful analysis.
Dont see a lot of 625 PSI type numbers in your list (just one at 730 PSI) of MAXIMUM perpendicular fiber stresses. You are not allowed to use the max numbers in design anyway. They are required to be derated for actual use. Many older houses did not derate (not required at the time) and the result is the sagging floors these old places now exhibit.chaz_oh
18 years agolast modified: 9 years ago"Dont see a lot of 625 PSI type numbers in your list (just one at 730 PSI) of MAXIMUM perpendicular fiber stresses. You are not allowed to use the max numbers in design anyway. They are required to be derated for actual use. Many older houses did not derate (not required at the time) and the result is the sagging floors these old places now exhibit."
But I see NO 50-100 numbers. Or anything close to 50. Nor the need to derate for the 48 hours needed to jack up a few joists.
It wouldn't be the compression strength causing the joists to sag in the middle. That would be 'modus of elasticity'.
I rest my case.
erasmus_gw
Original Author18 years agolast modified: 9 years agoI'd been wondering why nobody replied to my question about floor jacking, as I usually receive emails when someone replies to a post. Was surprised to check in here and find some replies.
Most people seem to think it is crucial to do the jacking very slowly, so now I've lost confidence in the house-moving guy who gave me an estimate. He thinks he can jack it up in a couple of hours.
What other kind of professional should I consult? I called a structural engineer but he didn't return my call.
We don't have plaster walls or ceilings..they're beaded wood and some are sheetrocked. The area that needs jacking has not been sheetrocked yet except for the ceiling. Previous owners wrecked the beaded wood with liquid nails which they had used to hang beaverboard.
It sounds like there's good reason to be nervous about jacking. Will be sure whoever does it has insurance at least. Or maybe we should just leave it alone and have a slanted floor.
chaz_oh
18 years agolast modified: 9 years agoThis might be too small of a job for that engineer. The one we used was a referral from a friend, and seemed reluctant to do such a small job. I think their rate was around $135/hour.
We ended up paying around $600 for some sketches, specs, and the all-important stamp on the plan. I probably could have found the information elsewhere, but felt the main girder holding up 2 floors wasn't something to scrimp on.
I would recommend a good contractor. Someone well established in the area. Some have architects on staff. They may call themselves a design/build firm. Yes, they might be a remodeling contractor. But that's what this is, isn't it?
Check them out with the local BBB, and talk to past customers. I would try to find out if they use hourly employees or subs. Hourly guys may take more time to a better job, as they might not be in a big rush to get done and get paid.
You could drive around and look for signs in yards where remodeling is going on. If they have a sign, they are probably licensed and have pulled a permit.
brickeyee
18 years agolast modified: 9 years ago"It wouldn't be the compression strength causing the joists to sag in the middle. That would be 'modus of elasticity'."
The point was the lack of derating is what allowed joists in older homes to sag.
Derating must seem like a strange requirement to you, but it is used to make sure structures stand long term.
It is not just modulus of elasticity for wood that causes problems. There is also fiber creep under long term loading. Wood is a very anisotropic material and has a completely different set of engineering issues compared to steel or concrete.
Even load bearing fasteners behave differently in wood since a nail is much harder than the wood it is driven into. Unlike a typical bolted joint in metal, all fasteners in a wood joint will share load without significant loss of strength.The building codes go to great lengths to specify allowable limits for materials in wood design. Woods are divided into a number of classes based on there usable range of loading. Designs are then required to use the class characteristic numbers. There is even machine stress rated lumber available with higher limits, but every piece has been measured.
Superbeam may still have a 30 day free license for trial use. You might want to mock up some wood designs to get an idea of the allowed limits and rules. A copy of the building codes and the standards for wood structure design be required reading also.Good luck in getting a PE to stamp off a set of jacking plans without on site supervision. I would not.
There are simply too many unknowns to formulate a set of plans to blindly follow without making them rather detailed and probably painful to even consider using. My license depends on making sure mistakes do not happen.A soil survey would be required to determine weight bearing capability. It is pretty unlikely the top surface of the ground will be suitable, so excavation will likely be required. It could be just a few inches, or maybe feet deep, to obtain suitable bearing. Generally existing concrete is not suitable for the point loading of jacks and either large timbers or steel beams are required to ensure adequate load spreading.
The loads are often difficult to determine, so over specification must be used to ensure margins. Add to this the distinct possibility that older houses often have structural loading that would not be acceptable today.
I have jacked many times to restore structures. Each job is a little different and requires careful engineering to come to a successful conclusion.
Even a simple floor sag over a basement can turn into a disaster if the supporting floor starts cracking from inadequate load spreading, and determining the allowable loads for 100+ year old concrete is guesswork at best. Assume very low strength and spread well more than you think is needed. Large footprint cribbing is required. I use sections (usually 3-4 feet long) of old railroad ties after careful inspection and removal of any seriously damaged portions (there is a reason the railroad yanked the ties).chaz_oh
18 years agolast modified: 9 years agoDerating doesn't seem strange at all. But it seems better applied in the electrical forum when running multiple THHN wires in 1/2" conduit, or how many dimmers you can install in a 3 gang box. Or perhaps an engineering forum when dealing with 10 story buildings. I would imagine derating is factored in to the requirements for a given application. But it is not a common builders term. The house mover doesn't have to know how many psi's the wood is rated at, but I'll bet he knows he'll need a larger base under the jack in soft soil. And I'll wager he doesn't get soil core samples before jacking up the house.
A more succinct and more easily understood answer might be to say one reason for the sagging joists could be that they were UNDERSIZED.
While your response is well-measured, it almost seems like a $2,000 answer to a $500 question.
My eyes began to glaze over with all the $5.00 words.
Many (most, I'd venture) old houses (this forum's focus) were built without having engineer's tables at their disposal. The fact that they are still standing tall and treasured by many is a testament to the builder's greatest engineering strength-common sense.
brickeyee
18 years agolast modified: 9 years ago"The fact that they are still standing tall and treasured by many is a testament to the builder's greatest engineering strength-common sense."
The problem is that the majority are not still standing. They came apart for one reason or another over the years.
Even in areas with many older (even back to the 1700s) structures, there are far more gone than are presently standing. Ever wonder why?While the detailed knowledge of derating and strengths of materials may not have been widely known 200-300 years ago, the Britich Navy had a great deal of hard earned knowledge about wood strengthsd and what woods to use were.
Most of the old houses in this forum probably were built using builders handbooks to give joist spans and sizing. The oldest one I own is dated 1820 or so.
A really cool one has listings for weight bearing floors. The 'planks are specified as 2 inches wide, and the table lists strengths and spans that appear crazy. Until you realize they are talking about factory floors and the 2 inch wide 'strips' are the narrow edge of 2x16, 2x18, even 2x30 inch boards. This is a Millers Fall MA buidling inspectors guide for mill buildings.SOrry if you are scared by big words. Try to get more education.
chaz_oh
18 years agolast modified: 9 years agoI think you'd be hard pressed to tell many of this forum's users that today's homes are built better than the oldies.
The highly engineered, stapled together waferboard crackerboxes that are being hastily thrown together today haven't withstood the test of time.
There are many reasons houses of old are no longer still standing. The main reason, I would believe, is neglect. Even oak timbers and 3/4" roof sheathing won't last if they are left to the elements.
As for being "scared by big words. Try to get more education."
What an effete snob. I'll bet you and your little buddies get a charge out of those kinds of remarks, as you sip your mocha java with extended pinkies down at Starbucks. The character Niles Crane comes to mind.
I'm hardly scared, nor am I unaware of their meanings. My point was, which your alleged mental acumen missed, was that this is not an engineer's forum. The poster asked a simple question about jacking up a sagging floor. What he got from you was an overblown thesis on the compressive strengths of wood, in which you were proven wrong, by the way.
To compare the requirements of temporary shoring with that of a typical structure is a bit of a stretch.
brickeyee
18 years agolast modified: 9 years agoI did not claim newer houses were built better. In many cases some older houses were overbuilt for the knowledge of the time and have remained. Many other built to the standards of the period have failed.
"What an effete snob. I'll bet you and your little buddies get a charge out of those kinds of remarks, as you sip your mocha java with extended pinkies down at Starbucks.:
I do not have any little buddies. I run a money making business restoring improving older houses. You brought up the "My eyes began to glaze over with all the $5.00 words."
Not me.I do not care if this is an engineering forum. Correct sizing of even temporary supports is how jobs are accomplished without those embarrassing failures.
Jacking up when the supporting timbers are undergoing compression failure form overloading prolongs the job and produces more damage to the structure than occurs with correctly sized and supported repairs."in which you were proven wrong, by the way."
You are dead wrong. The typical allowable load on wood is between 1/5 and 1/10 of the ultimate load. Temporary bracing is still required to meet all the load limits for permanent use. Sorry if the codes bother you and you are ignorant of the requirements.
One of the greatest problems in these jobs is determining what the actual loads are. Without drawings it requires some careful detective work and analysis.I have been called in a number of times to finish up the work started by a GC with little engineering knowledge who has had a temporary support fail, or even a concrete slab punch through from point overloading.
I have also testified in court about these failures.The loads involved in jacking even joists can reach levels that cause compression failure of undersized jack supports. After you have been doing the work for 20+ years, let me know how your calculations have faired.
I have a PE seal that I guard very carefully, since ay problems will always come back to me. I stamped the plans as safe.chaz_oh
18 years agolast modified: 9 years agoWell, I have been in the construction business for nearly 30 years, and have never seen nor experienced one of these "failures", although I'm sure some do occur.
It was an engineering firm that OK'd the flight of the space shuttle Challenger.
Somewhere along the line, it was an engineer that signed off on the plans to build the houses in New Orleans, below sea level.
It was an engineer that designed the levee.......
So the PE seal doesn't mean that much to me. I'm sure you are competent at your occupation. But master builders have been producing fine structures for thousands of years, all without the blessing of some PE.
erasmus_gw
Original Author18 years agolast modified: 9 years agoWell, one of you suggested that I just hire a contractor with a sign in someone's yard. I had a terrible large -scale house disaster hiring a contractor even though I checked out his references and insurance. It sounds like an engineer wouldn't want to mess with house jacking. ??
So, we might do this ourselves.Now, I've had a couple of people tell me, including the house mover, that concrete cap blocks would be enough to support the jacks on. But it sounds like Brickeye thinks we might need to dig down to harder ground, though the dirt floor of our crawlspace seems pretty firm. I don't know how to tell how firm it should be. Seems like if the concrete cap block settled down into the ground it might be possible to just put another cap block on top of it and try again. ?? My kitchen floor needs to be jacked up only about an inch.
We got some inexpensive floor jacks from Lowe's or Home Depot. ARe those usually good enough or should I look for heavier duty jacks?
brickeyee
18 years agolast modified: 9 years agoHey chaz oh,
Every one of those span tables you use was generated by a PE.
Every highway bridge, bulding over about 2 floors, or commercial structure is reviewed by a PE.
NASA does not put much weight in PE expertise and rarely uses them for anything. Being the government they are exempt.
You may not have much respect, but I testify in court against the yahoos who guess at all sorts of things and cause problems. It gets pretty lucrative when there is a lot of half-a$$ work going on.
Jack away on a lousy bearing surface. Sooner or latter you will be facing a PE in court and you will loose.
When I encounter a soil problem I am not sure if, in comes a geotechnical engineer.
When a design gets past anything I am not comfortable with I have a structural to call on (I rarely do cantilevers without his review).
When they need Manual J for HVAC, or electrical work they call me if they are not sure.
A PE is responsible for anything they seal off on for darn near forever. Contractors disappear in the wind at the first hint of serious problems.
I had a case a few years ago with a well driller who failed to check the data for limestone and caverns in the area. The sink-hole cost him his business and his insurance company over $1M.
Most homebuilding is overdone enough that problems do not occur (the PEs checked all the stud tables and span tables). Older buildings cause a lot of problems with inadequate design.natenh
16 years agolast modified: 9 years agoMy question is whether to use steel or 10x10 hemlock beams to jack up a 22X24 oak timber frame outbuilding.The building needs to be jacked up enough to cut away the bottom section, then lowered onto cement pilings.Also, can the jacking beams only support the interior frame or does the sill/side wall have to be supported at the same time? Thanks.
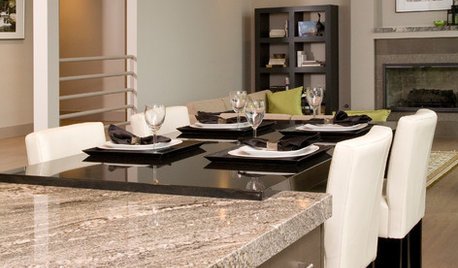
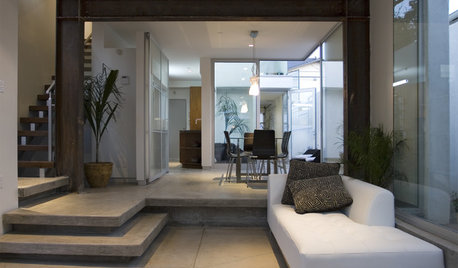
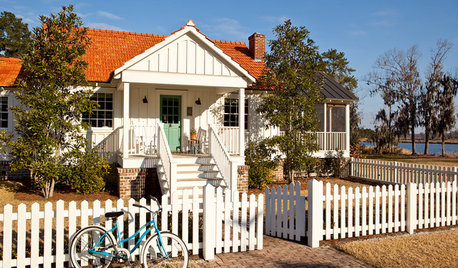
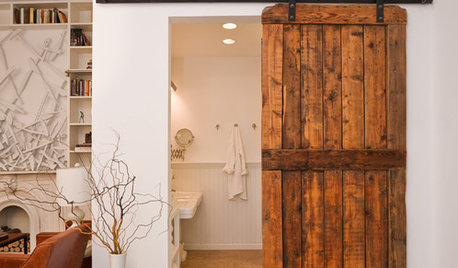
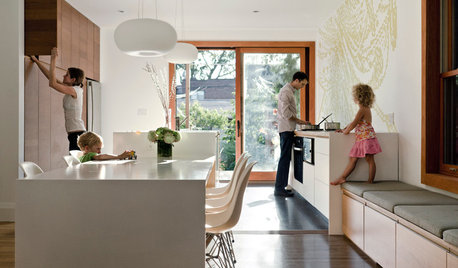
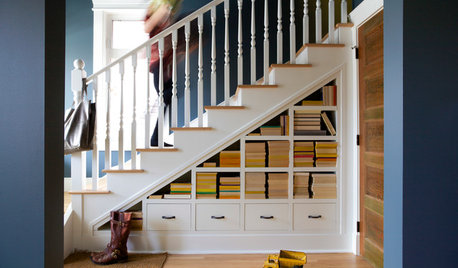
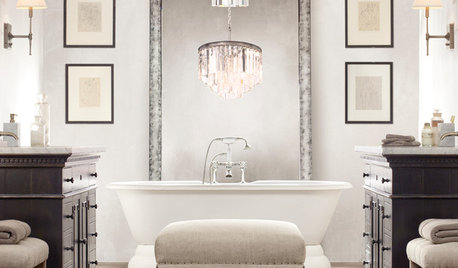
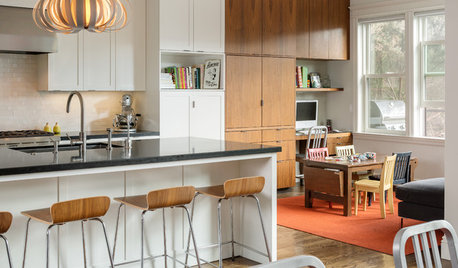
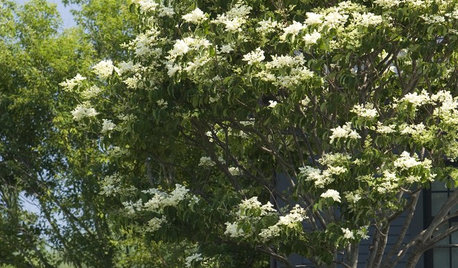
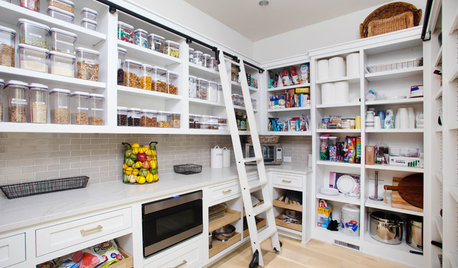
tanama