I asked for CLEAR poly, got darker floors...
bronwynspetalpatch
10 years ago
Related Stories
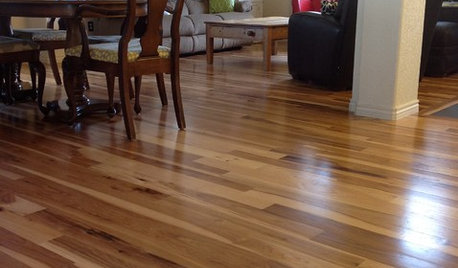
MATERIALSWhat to Ask Before Choosing a Hardwood Floor
We give you the details on cost, installation, wood varieties and more to help you pick the right hardwood flooring
Full Story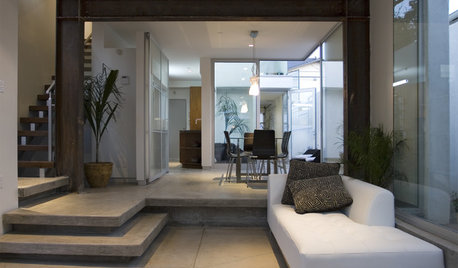
GREEN BUILDINGConsidering Concrete Floors? 3 Green-Minded Questions to Ask
Learn what’s in your concrete and about sustainability to make a healthy choice for your home and the earth
Full Story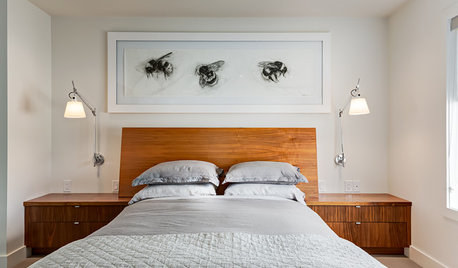
BEDROOMSNew This Week: 3 Bed, Nightstand and Wall Combos You’ve Got to Try
Whether you prefer moody, minimalist or sunny, these 3 bedrooms uploaded to Houzz recently are exercises in stylish harmony
Full Story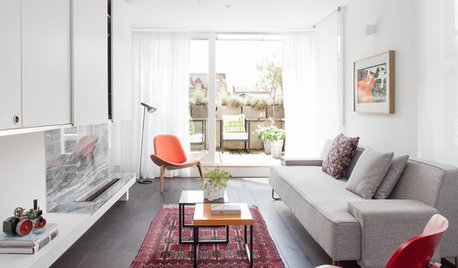
DECORATING GUIDESAsk an Expert: How to Decorate a Long, Narrow Room
Distract attention away from an awkward room shape and create a pleasing design using these pro tips
Full Story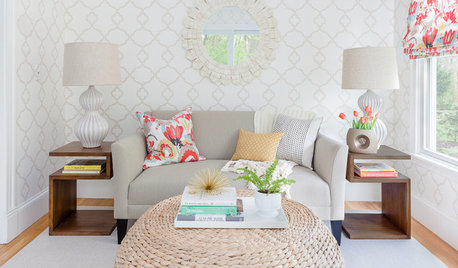
DECORATING GUIDESAsk an Expert: How to Decorate a Small Spare Room
It can be difficult to know what to do with that tiny extra room. These design pros offer suggestions
Full Story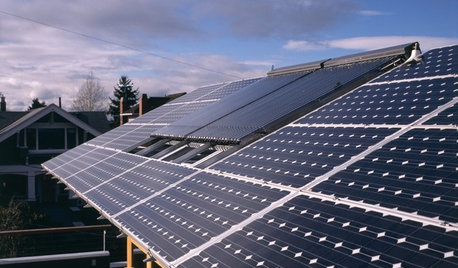
GREEN BUILDINGLet’s Clear Up Some Confusion About Solar Panels
Different panel types do different things. If you want solar energy for your home, get the basics here first
Full Story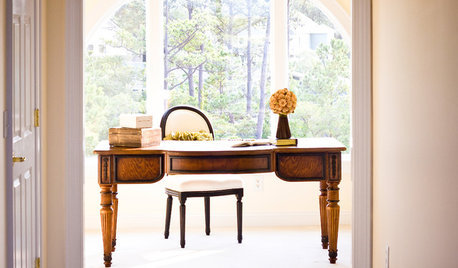
HOUSEKEEPINGGot a Disastrously Messy Area? Try Triage
Get your priorities straight when it comes to housekeeping by applying an emergency response system
Full Story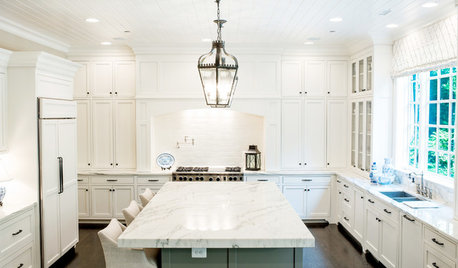
KITCHEN CABINETSHold Everything — Your White Kitchen Cabinets Just Got Better
These design moves will add even more to white kitchen cabinets’ appeal
Full Story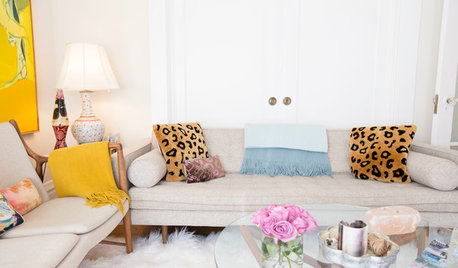
ECLECTIC STYLESee How a Bright Victorian Apartment Got Its Collected Look
Arriving in San Francisco with little but a chair and bed, a couple hits on an interior style that feels collected over time
Full Story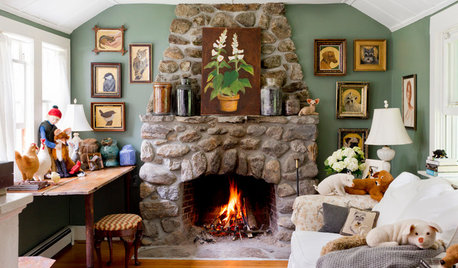
HOUSEKEEPINGBefore You Roast Those Chestnuts, Make Sure You've Got a Clean Chimney
Here's how to ensure your chimney is safe for holiday gatherings by the fire
Full Story
bronwynspetalpatchOriginal Author
glennsfc
Related Professionals
University City Flooring Contractors · American Fork Flooring Contractors · Bossier City Flooring Contractors · Brandon Flooring Contractors · Greenville Flooring Contractors · Homestead Flooring Contractors · Raleigh Flooring Contractors · Broadview Heights General Contractors · Buena Park General Contractors · Dothan General Contractors · Erlanger General Contractors · Oneida General Contractors · Panama City General Contractors · San Marcos General Contractors · Seabrook General Contractorsgregmills_gw
bronwynspetalpatchOriginal Author
gregmills_gw
bronwynspetalpatchOriginal Author
GreenDesigns
bronwynspetalpatchOriginal Author
User
gregmills_gw
glennsfc
susanlynn2012
bronwynspetalpatchOriginal Author
bronwynspetalpatchOriginal Author
susanlynn2012
bronwynspetalpatchOriginal Author
glennsfc
gregmills_gw
User
bronwynspetalpatchOriginal Author
bronwynspetalpatchOriginal Author
glennsfc
live_wire_oak
glennsfc
knot2fast
bronwynspetalpatchOriginal Author
User