no expansion gap in hardwood floors
threeberries
11 years ago
Featured Answer
Sort by:Oldest
Comments (15)
User
11 years agoattofarad
11 years agoRelated Professionals
Cambridge Flooring Contractors · Marietta Flooring Contractors · Oregon City Flooring Contractors · Waunakee Flooring Contractors · West Linn Flooring Contractors · Big Lake General Contractors · Dardenne Prairie General Contractors · Green Bay General Contractors · Jackson General Contractors · Kentwood General Contractors · Merritt Island General Contractors · Pico Rivera General Contractors · Rolla General Contractors · Rosemead General Contractors · Syosset General Contractorsthreeberries
11 years agogregmills_gw
11 years agobrickeyee
11 years agothreeberries
11 years agoglennsfc
11 years agobrickeyee
11 years agothreeberries
11 years agobrickeyee
11 years agoUNancy
10 years agolazy_gardens
10 years agoglennsfc
10 years agoBarbara Zell
3 years ago
Related Stories
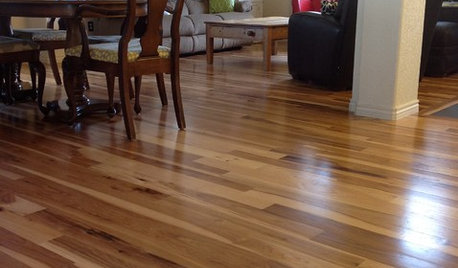
MATERIALSWhat to Ask Before Choosing a Hardwood Floor
We give you the details on cost, installation, wood varieties and more to help you pick the right hardwood flooring
Full Story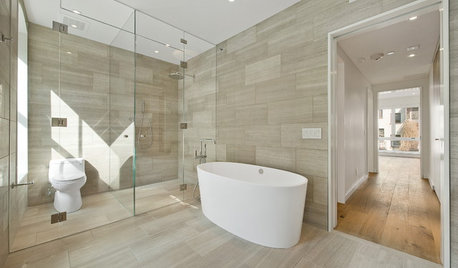
REMODELING GUIDESTransition Time: How to Connect Tile and Hardwood Floors
Plan ahead to prevent unsightly or unsafe transitions between floor surfaces. Here's what you need to know
Full Story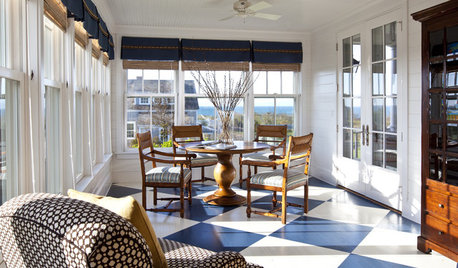
FLOORSHow to Paint Your Hardwood Floors
Know how to apply nail polish? Then you can give your wooden floors a brand-new look
Full Story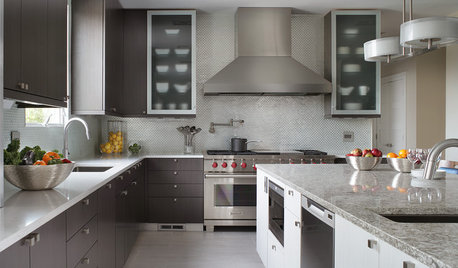
BEFORE AND AFTERSKitchen Expansion Is a Crowd Pleaser
A modern makeover and clever new layout make this New Jersey kitchen a hotspot for friends and family
Full Story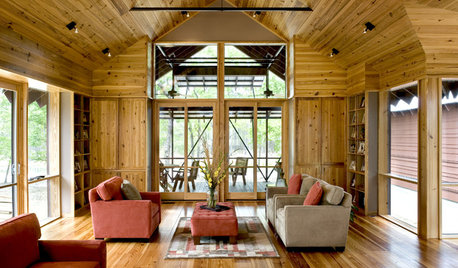
HOUZZ TOURSHouzz Tour: From Overgrown Weeds to Picturesque Farmhouse Expanse
This once-neglected 100-acre South Carolina site now features a lake, a wood-filled farmhouse and a far-reaching view
Full Story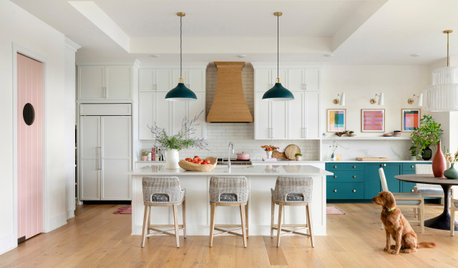
HOUSEKEEPINGHow to Clean Hardwood Floors
Gleaming wood floors are a thing of beauty. Find out how to keep them that way
Full Story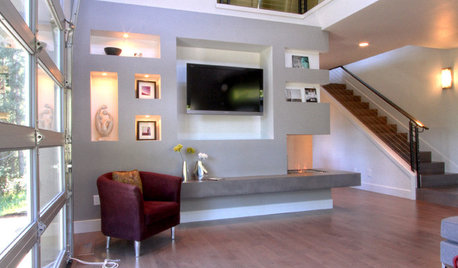
REMODELING GUIDESContractor Tips: Smooth Moves for Hardwood Floors
Dreaming of gorgeous, natural wood floors? Consider these professional pointers before you lay the first plank
Full Story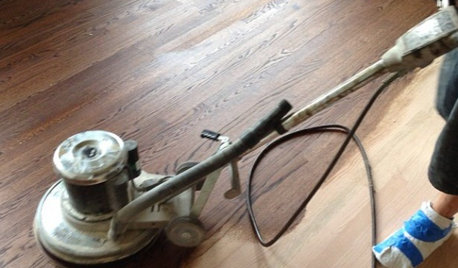
GREAT HOME PROJECTSWhat to Know Before Refinishing Your Floors
Learn costs and other important details about renewing a hardwood floor — and the one mistake you should avoid
Full Story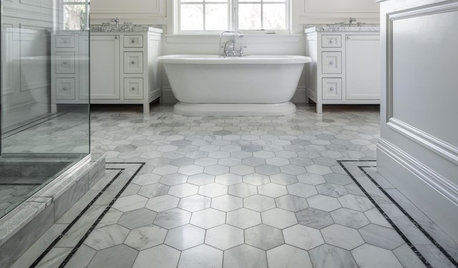
TILEWhy Bathroom Floors Need to Move
Want to prevent popped-up tiles and unsightly cracks? Get a grip on the principles of expansion and contraction
Full Story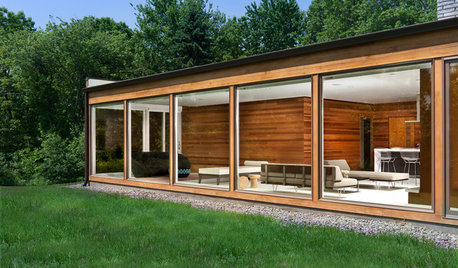
HOUZZ TOURSHouzz Tour: Let's Be Transparent Here
Expansive glass and a new floor plan celebrate a midcentury modern home's openness and connection to nature
Full Story
nepool