Spray Foam Insulation Question
Jen
10 years ago
Related Stories
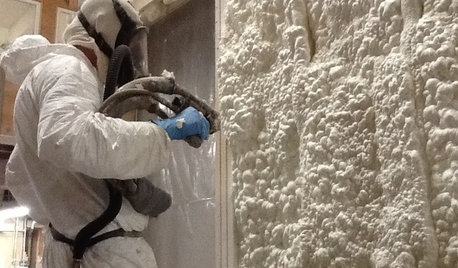
MATERIALSInsulation Basics: What to Know About Spray Foam
Learn what exactly spray foam is, the pros and cons of using it and why you shouldn’t mess around with installation
Full Story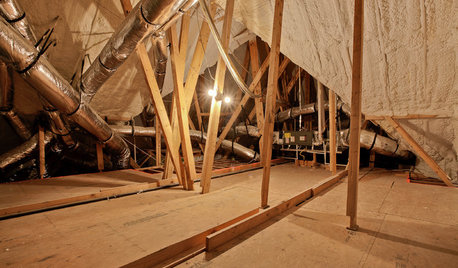
GREEN BUILDINGEcofriendly Cool: Insulate With Wool, Cork, Old Denim and More
Learn about the pros and cons of healthier alternatives to fiberglass and foam, and when to consider an insulation switch
Full Story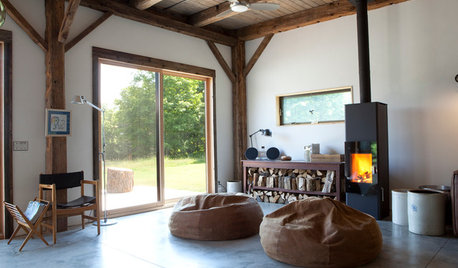
GREEN BUILDINGInsulation Basics: Heat, R-Value and the Building Envelope
Learn how heat moves through a home and the materials that can stop it, to make sure your insulation is as effective as you think
Full Story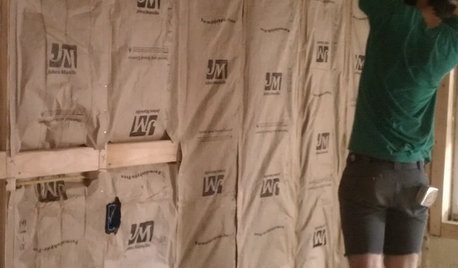
REMODELING GUIDESCool Your House (and Costs) With the Right Insulation
Insulation offers one of the best paybacks on your investment in your house. Here are some types to discuss with your contractor
Full Story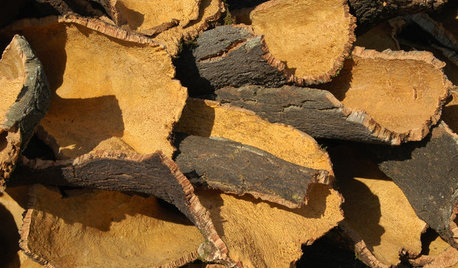
GREEN BUILDINGInsulation Basics: Natural and Recycled Materials
Consider sheep’s wool, denim, cork, cellulose and more for an ecofriendly insulation choice
Full Story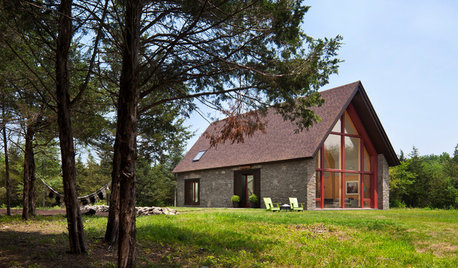
GREEN BUILDINGInsulation Basics: Designing for Temperature Extremes in Any Season
Stay comfy during unpredictable weather — and prevent unexpected bills — by efficiently insulating and shading your home
Full Story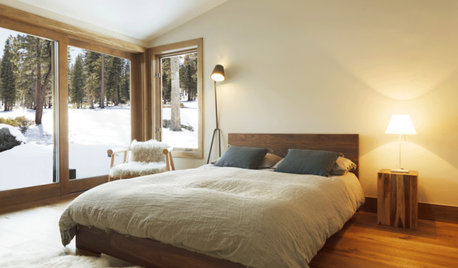
WINDOW TREATMENTSEasy Green: 9 Low-Cost Ways to Insulate Windows and Doors
Block drafts to boost both warmth and energy savings with these inexpensive but effective insulating strategies
Full Story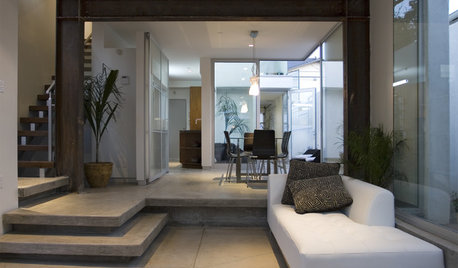
GREEN BUILDINGConsidering Concrete Floors? 3 Green-Minded Questions to Ask
Learn what’s in your concrete and about sustainability to make a healthy choice for your home and the earth
Full Story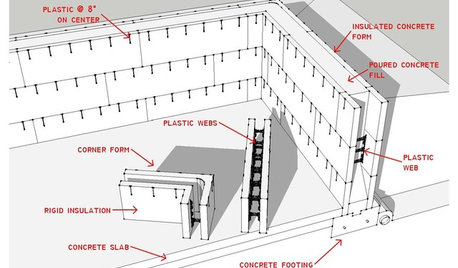
KNOW YOUR HOUSEKnow Your House: The Basics of Insulated Concrete Form Construction
Get peace and quiet inside and energy efficiency all around with this heavy-duty alternative to wood-frame construction
Full Story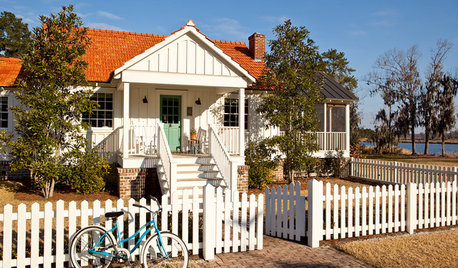
REMODELING GUIDESConsidering a Fixer-Upper? 15 Questions to Ask First
Learn about the hidden costs and treasures of older homes to avoid budget surprises and accidentally tossing valuable features
Full Story
JenOriginal Author
LOTO
Related Professionals
Baltimore Architects & Building Designers · North Chicago Architects & Building Designers · Universal City Architects & Building Designers · Winchester Architects & Building Designers · Accokeek Home Builders · Beavercreek Home Builders · Eagan General Contractors · New Bern General Contractors · Arizona City General Contractors · Country Club Hills General Contractors · Jericho General Contractors · Lakeside General Contractors · Newington General Contractors · Panama City Beach General Contractors · Spanaway General Contractorsddr000
worthy
War_Eagle
ddr000
ddr000
War_Eagle
manhattan42
LawPaw
Brian_Knight
Brian_Knight
JenOriginal Author
momto3kiddos
Brian_Knight
david_cary
dekeoboe
energy_rater_la
LawPaw
energy_rater_la
LawPaw
mousje.711
energy_rater_la
want2build