ICF Construction
dreambuilder
11 years ago
Related Stories
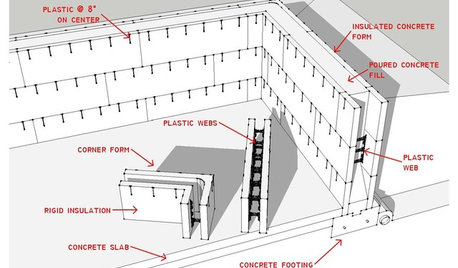
KNOW YOUR HOUSEKnow Your House: The Basics of Insulated Concrete Form Construction
Get peace and quiet inside and energy efficiency all around with this heavy-duty alternative to wood-frame construction
Full Story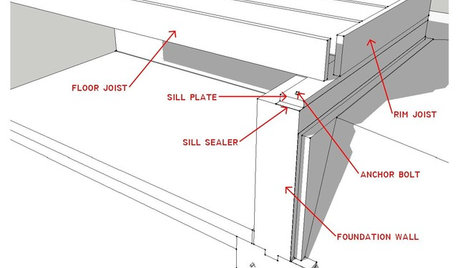
KNOW YOUR HOUSEKnow Your House: What Makes Up a Floor Structure
Avoid cracks, squeaks and defects in your home's flooring by understanding the components — diagrams included
Full Story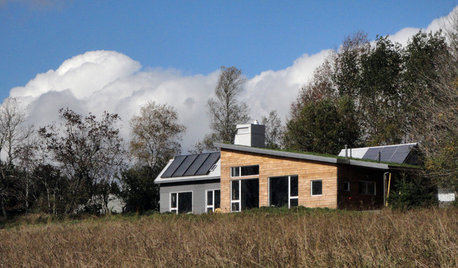
GREEN BUILDINGHouzz Tour: Going Completely Off the Grid in Nova Scotia
Powered by sunshine and built with salvaged materials, this Canadian home is an experiment for green building practices
Full Story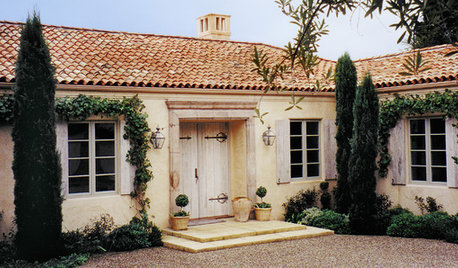
REMODELING GUIDES8 Natural Home Materials That Can't Be Beat
See how designing with natural stone, clay, wood and more can give a house luminosity, depth of color and lasting appeal
Full Story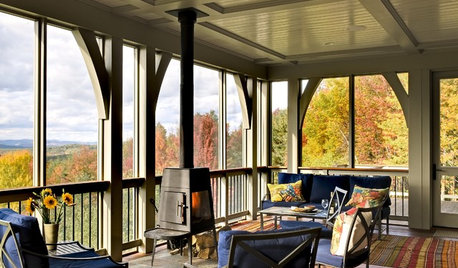
Houzzers Say: A Wish List for the Entire House
10 dreamy suggestions to help a home meet all of your present and future needs
Full Story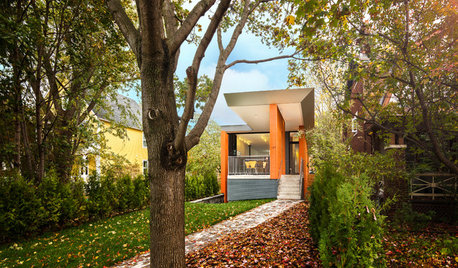
MODERN HOMESHouzz Tour: A Modern Home Rooted in Its Place
It's partially buried in the earth, but with a cantilevered roof and strong colors, this Ottawa home is anything but shy
Full Story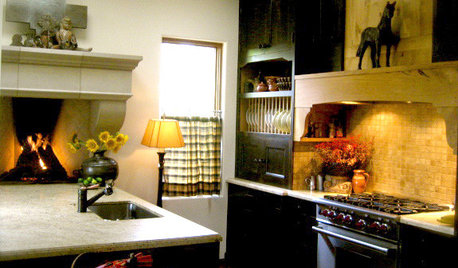
KITCHEN DESIGNKitchen of the Week: Warm Up By the Fire
Dark cabinetry, warm woods, and a counter-height hearth make this Portland kitchen special
Full Story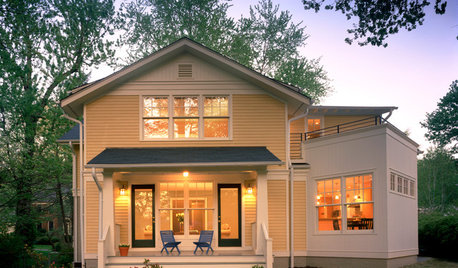
WORKING WITH PROSHow to Hire the Right Architect: Comparing Fees
Learn common fee structures architects use and why you might choose one over another
Full Story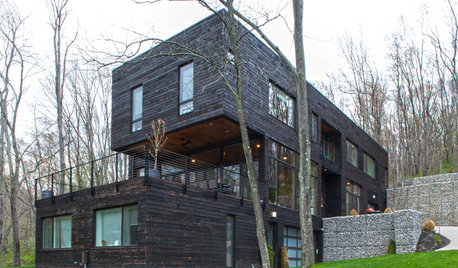
HOUZZ TOURSMy Houzz: Modernism Takes a Natural Turn in Pennsylvania
Generous wood throughout and woodsy sights outdoors soften and warm this home’s modern lines
Full Story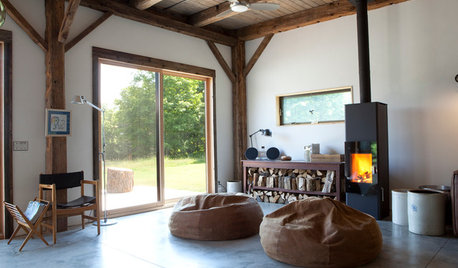
GREEN BUILDINGInsulation Basics: Heat, R-Value and the Building Envelope
Learn how heat moves through a home and the materials that can stop it, to make sure your insulation is as effective as you think
Full Story
flgargoyle
andry
Related Professionals
Suamico Design-Build Firms · Kaysville Home Builders · Reedley Home Builders · Three Lakes General Contractors · Belleville General Contractors · Bloomington General Contractors · Dardenne Prairie General Contractors · Greenville General Contractors · Hampton General Contractors · Merrimack General Contractors · Palestine General Contractors · Seal Beach General Contractors · Spanaway General Contractors · Williamstown General Contractors · Winfield General ContractorsEpiarch Designs