Advanced framing - other considerations
dadereni
10 years ago
Related Stories
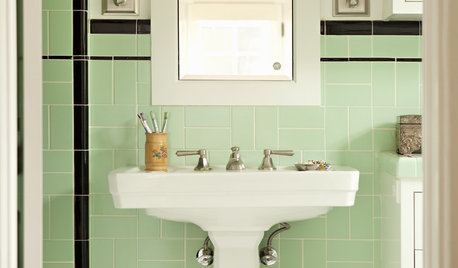
BATHROOM DESIGN9 Surprising Considerations for a Bathroom Remodel
Don't even pick up a paint chip before you take these bathroom remodel aspects into account
Full Story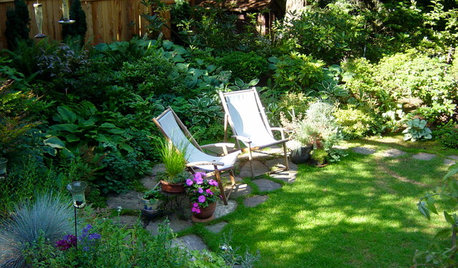
LANDSCAPE DESIGN5 Essential Considerations for a Landscape Design Project
Get your winter garden fix by planning an entirely new landscape or just an update for a single garden stretch
Full Story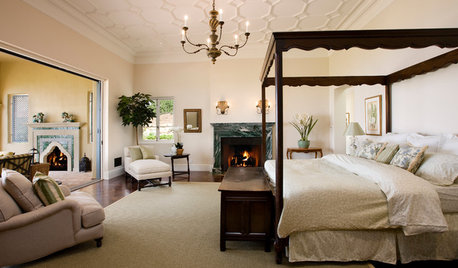
ADDITIONS10 Considerations for the Bedroom Addition of Your Dreams
Get the master bedroom you've always wanted by carefully considering views, access to the outdoors and more
Full Story
WINDOWSSteel-Framed Windows Leap Forward Into Modern Designs
With a mild-mannered profile but super strength, steel-framed windows are champions of design freedom
Full Story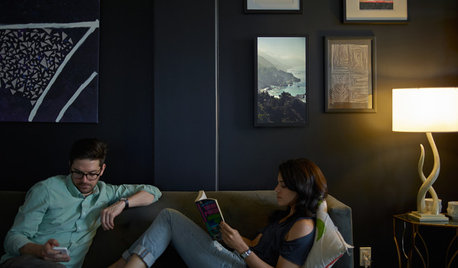
HOME TECHIs the Timing Finally Right for Framed Digital Art?
Several companies are preparing to release digital screens and apps that let you stream artworks and video on your wall
Full Story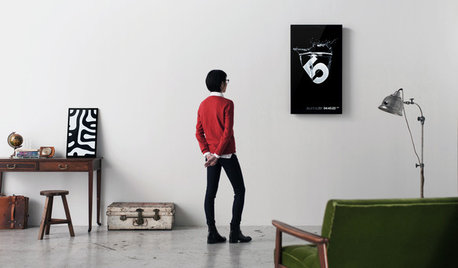
ARTNew Digital Art Frame Gets Put to the Test
Our writer sets up the EO1 at home, then invites artist friends over for a look — at images of their own work. See what they have to say
Full Story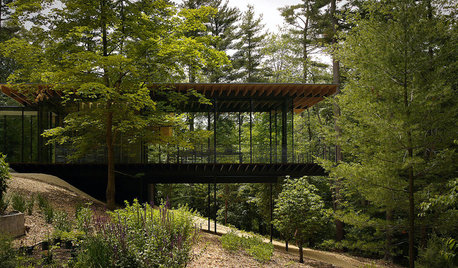
ARCHITECTUREDesign Workshop: The Intriguing Effects of Exposed Framing
Reveal the structure of your home for interesting design opportunities and eye-catching visual effects
Full Story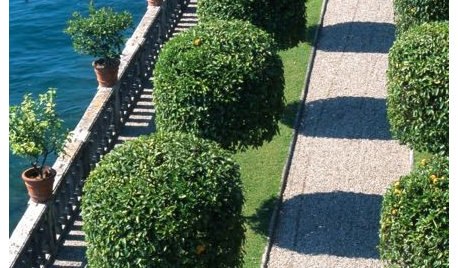
LANDSCAPE DESIGN5 Structural Plants to Frame Your Garden Beautifully
Consider these trees and shrubs live building blocks, providing structure and definition in even a small garden
Full Story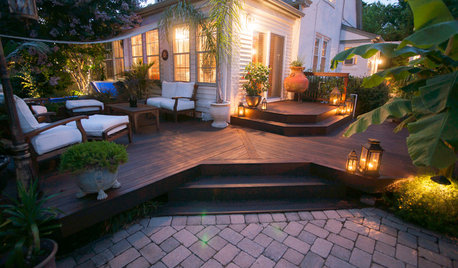
MOST POPULARWhat to Know About Adding a Deck
Want to increase your living space outside? Learn the requirements, costs and other considerations for building a deck
Full Story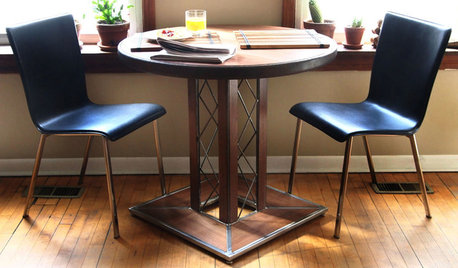
LIFEHow to Navigate an Extended Guest Stay
Keep sharing living quarters a positive experience by pondering the answers to these questions in advance
Full Story
Brian_Knight
User
Related Professionals
Asbury Park Architects & Building Designers · Aliso Viejo Home Builders · Angleton Home Builders · Forest Hill Home Builders · Holiday Home Builders · Ashtabula General Contractors · Cottage Grove General Contractors · Erie General Contractors · Fitchburg General Contractors · Goldenrod General Contractors · La Marque General Contractors · Modesto General Contractors · Perrysburg General Contractors · Rolling Hills Estates General Contractors · Rosemead General Contractorsenergy_rater_la
Epiarch Designs