please help with insulation questions
Karen.1288
11 years ago
Related Stories
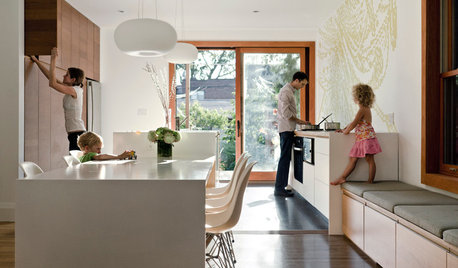
GREEN DECORATING8 Questions to Help You See Through Green Hype
With the ecofriendly bandwagon picking up some dubious passengers, here's how to tell truly green products and services from the imposters
Full Story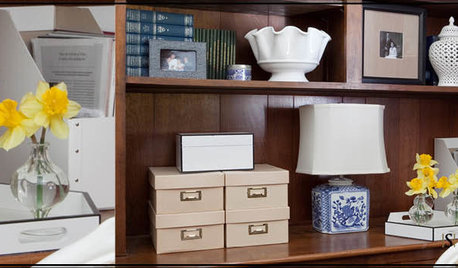
ORGANIZING4 Questions to Help You Organize Your Favorite Photos
Organize your keeper photos with a system that's just right for you, whether it's in the cloud or you can hold it in your hand
Full Story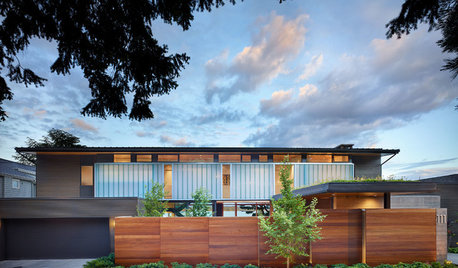
CURB APPEAL7 Questions to Help You Pick the Right Front-Yard Fence
Get over the hurdle of choosing a fence design by considering your needs, your home’s architecture and more
Full Story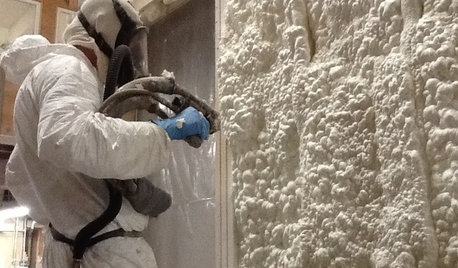
MATERIALSInsulation Basics: What to Know About Spray Foam
Learn what exactly spray foam is, the pros and cons of using it and why you shouldn’t mess around with installation
Full Story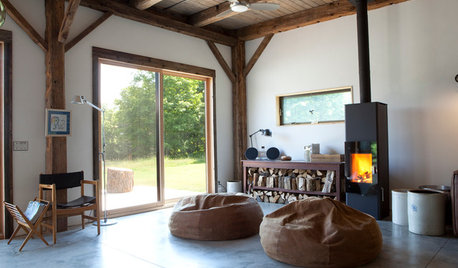
GREEN BUILDINGInsulation Basics: Heat, R-Value and the Building Envelope
Learn how heat moves through a home and the materials that can stop it, to make sure your insulation is as effective as you think
Full Story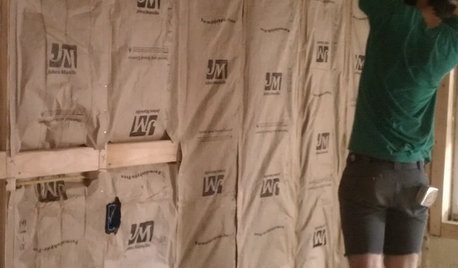
REMODELING GUIDESCool Your House (and Costs) With the Right Insulation
Insulation offers one of the best paybacks on your investment in your house. Here are some types to discuss with your contractor
Full Story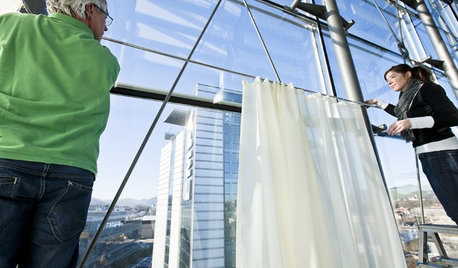
HOME OFFICESQuiet, Please! How to Cut Noise Pollution at Home
Leaf blowers, trucks or noisy neighbors driving you berserk? These sound-reduction strategies can help you hush things up
Full Story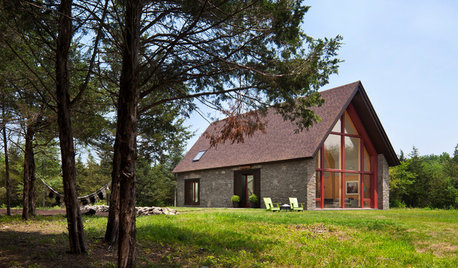
GREEN BUILDINGInsulation Basics: Designing for Temperature Extremes in Any Season
Stay comfy during unpredictable weather — and prevent unexpected bills — by efficiently insulating and shading your home
Full Story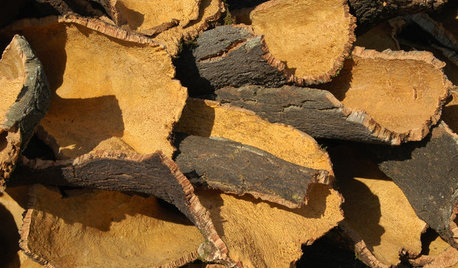
GREEN BUILDINGInsulation Basics: Natural and Recycled Materials
Consider sheep’s wool, denim, cork, cellulose and more for an ecofriendly insulation choice
Full Story
Annie Deighnaugh
energy_rater_la
Related Professionals
Bull Run Architects & Building Designers · Morganton Architects & Building Designers · Portage Architects & Building Designers · Royal Palm Beach Architects & Building Designers · Commerce City Home Builders · Montebello Home Builders · West Whittier-Los Nietos Home Builders · Galena Park General Contractors · Alabaster General Contractors · Bon Air General Contractors · Gloucester City General Contractors · Markham General Contractors · Titusville General Contractors · Welleby Park General Contractors · Avenal General ContractorsKaren.1288Original Author
energy_rater_la
Epiarch Designs
User
Annie Deighnaugh
david_cary
Epiarch Designs
Epiarch Designs
david_cary
Epiarch Designs
renovator8
brickeyee
energy_rater_la
david_cary
Epiarch Designs