XPS, Please answer, once and for all!!!!
Worthy and others with experience....
You who have the experience over 20 years or so, let me ask this one final time as it really has me worked up. If $$$$ were no object I'd just do the XPS thing. Why do I need XPS at all. Other than the home building something or other reccomends it...WHY? I am not trying to be snippy here, I really want to understand and I do not.
If I have NEVER had any visible water seeping thru the walls and its never very damp in the basement (we do run a humidifier but it even cycles on and off)...why XPS? What would be wrong with constructing a 2 X 4 wall and inch or two from the concrete and insulating the wall with fiberglass batts, kraft paper towards the inside of the room, ie against the drywall. In other words NOTHING would be touching the concrete at all. I can not imagne how water or mositure would permiate tow the fiberglass an inch or two away. The fiberglass is already suppose to be mositure resistant any way. Can you explain the pratcicality of it...? Does adding the wall and creating, essentially a 1 to 2 inch space around the perimeter of the room ADD to the possibility of mositure? If so, where would this mositure be present.
I really do not want to take the word of neighbors OR folks who have given me estimated to add some walls in the basement. But all seem to feel XPS is a luxory not necesary...at least in Eastern PA...
I just want to understand what COULD happen if I do not use it and what the chances of that are....
Comments (40)
worthy
15 years agoDon't feel bullied here! It's your home and you can do what you want! Just as you can take the advice of your neighbours and local contractors over the leading building scientists in the US and Canada.
The method you want to use may even meet Code in your area.
As I've mentioned, I used to insulate essentially that way too. And lived in those homes with no evident problems. That I used a dehumidifier summer and winter probably helped put off problems. (But I bet if I ripped down the drywall now, I would see mould growth and rot.)
Keeping the fiberglass off the concrete wall will keep it away from the moisture that will condense on the wall during the winter as warm air finds its way through the drywall. In the summer, as the warm vapour laden air goes in the other direction--towards the cooler basement interior--it will be trapped behind any vapour barrier you use. As well, the air currents swirling in the space between the insulation and the wall will reduce the R Value of the FG.
XPS virtually eliminates the chance of getting mould and rot and provides a much higher real R-Value (as opposed to the nominal R Value you will get from using fg the way you propose.)
You could still use FG if you use a reversible vapour barrier called Membrain. But Membrain is more expensive than kraft batts or poly. I have no personal experience with Membrain as it was only recently approved here.
Here is a link that might be useful: Building Science
andrelaplume2
Original Author15 years agonow we are getting somewhere. In the winter warmer air in the basement will get thru the drywall, fiberglass and make its way to the concrete where it will condense..right!
So:
I do not see this occurring now; perhaps the new wall will haten or encourage this. Assume it happens. The mositure is on the concrete right..or is it travelling thru the air as vapor? It is not touching anything if its only on the concrete so what will rot? Where would mold grow?
Related Professionals
DeRidder General Contractors · Meadville General Contractors · Mount Laurel General Contractors · Rosemead General Contractors · Selma General Contractors · Summit General Contractors · Tabernacle General Contractors · Five Corners Architects & Building Designers · Honolulu Flooring Contractors · Livonia Flooring Contractors · Mukilteo Flooring Contractors · Oceanside Flooring Contractors · Stockton Flooring Contractors · Sun City Flooring Contractors · University Park Flooring Contractorsworthy
15 years agoIf the basement isn't finished, the temperature variation usually isn't great enough for condensation
Without a warm side vapour barrier in the winter, water vapour will pass through the wall and condense on the cold concrete, run down the wall and go somewhere--under the plate for instance. In the summer, water vapour will pass through to the finished area with no problem.
With a warm side vapour barrier:
Works fine in the winter. But in the summer the water vapour will condense and run down the vapour barrier inside the wall and cause mould and mildew. BTW, fiberglass is water resistant and doesn't support mould. But the mould grows on all the things inevitably trapped in the fiberglass, from drywall dust to dropped human cells picked up when it was installed. Plus the mould feeds on the backside of the drywall and the wood.With vapour barriers on both sides of the drywall, a system that many builders use water vapour is trapped between the vapour barriers and feeds mould. Even the tightest vapour barriers have leaks and the barriers themselves are still permeable.
worthy
15 years agoAs the picture below illustrates, mould can grow quite well on the interior foundation wall with virtually no obvious food source.
Mould and moisture expert Daniel Feldman notes that "Preliminary data shows that very often I find severe Aspergillus sp. or Penicillium sp. infection of fiberglass over damp crawl spaces and in damp building walls against below-grade foundations, even when there is no mold actually visible on the insulation or its kraft paper facing. On below-grade building walls that are to be insulated I prefer solid foam insulating board as it does not hold moisture and is less mold-friendly."
Mould growing on a basement block wall.
Here is a link that might be useful: Mold prevention
andrelaplume2
Original Author15 years agoso with XPS, in the winter, the cold will pass thru the wall (drywall vapor barrier / insulation and NOT condense on the XPS?
in the summer guess it stops heat from getting in to condense on the kraft backed insulation.
I admit I am suspicious but maybe I should hold off until I can afford it.
The cheapest formular pink stuff at HD is 3/8 X 4 X 50. I think its meant as a house wrap. I do not suppose I could use this? Next option would be either 1/2" or 3/4" but damn it gets pricey!
worthy
15 years agoWhy not consider Wallmate or equivalent? It's XPS, but you don't have to build a separate stud wall for the drywall. That can be quite a savings in materials and time for a top flight insulation method.
If you're planning to stay awhile, I'd go with at least 2" XPS if you're in the cold part of eastern Pennsylvania. See hygrothermic map.
XPS has low permeability, so in the summer, when the water vapour is trying to move from the high temperature outside to the low temp basement it impedes that flow to an amount that can be handled safely. See Yost and Lstiburek, "Basement Insulation Systems" at Building Science.
Correction: previous post said vapour barriers on both sides of the drywall It should have read "on both sides of the insulation". [It would be really helpful if there were an "edit" function here.]
Hygrothermic Map
Here is a link that might be useful: Installing Wallmate (Scroll down to Interior Basement)
andrelaplume2
Original Author15 years agoI watched the video and it almost looked too easy! I am unsure what those screws are...I bet they do not go into the concrete as easy as it looks. Of course running outlets and switched is pain and God forbid you ever need to run a wire later. Still for the area I am thinking about it is worth considering...I'll need to see the cost.
By the way...where does one find those panels?
worthy
15 years agoHow you handle electrical will depend on local codes and personal preferences. For instance, you may have to use BX cable; shallow boxes may not be permitted etc. In any case, you can always use approved surface-mount conduit and boxes.
where does one find those panels?
In the US, call 1-866-583-2583 for information on the distributors nearest to you.
andrelaplume2
Original Author15 years agoUpdate, they do not appear to sell Wallmate at my HD or Lowes although Lowes did just get in 1/2 X 4 X 8 Dow blueboard, R3, sheathing...says for foundations and such....said Styrofoam and the sheet. The price was at least within reason ($10) a sheet. Would this suffice? Glue (?) this to exterior walls then frame up against it with kraft fiberglass?
Finally, and I think I have now been 'scared' into putting some type of foam up anyway BUT a contractor / friend looked at what I was trying to accomplish and understood the considered the moisture potential of in effect having a sealed 2" space around the perimeter of the basement.
He was not convinced there would be moisture issues but admitted he was not a scientist! He pointed out in my case though that the space behind the wall would easily 'breath' since I would not actually be sealing the entire perimter. I would have open concrete wall space in a 12 foot unfinished closet (too many pipes and stuff to frame around) He thought the air would naturally flow in / out of the closet then to the left and right framed walls around it. A similar situation would exist on an opposite wall. Again, he said it was my $$$ to spend but would not sweat it. (Ironic term)
So, about that 1/2" dow stuff at Lowes..a reasonable compromise? If not I need to know what you think is the safest methid to frame out without the foam....just to expensive otherwise.
andrelaplume2
Original Author15 years ago..we have a marketplace at work (online) ..person overbought and is selling what he descibes as 4 X 8 X 1 sheets of white foam board (R value 1.5 he thinks) with foil on each side. I wonder if the foil is easily removed....
I think I am going to take another look at the DOW 1/2 styrofoam too...I hope that will suffice...no?
worthy
15 years agoFrom Yost & Lstiburek "Basement Insulation Systems" (linked previously) describing a University of Waterloo study:
"Walls with 3.5 inches of extruded polystyrene (XPS) and no vapor barrier performed the best in this analysis. However, walls with 0.75 inches of extruded polystyrene and 3.5 inches of fiberglass batt insulation in the cavity would perform well as long as interior humidity was controlled below 50 percent during the summer. Increasing the extruded polystyrene to 1.0 or 1.5 inches would improve performance even with higher interior relative humidity during the summer months. This part of the analysis assumed that the concrete wall had a relative humidity of 100 percent at the exterior temperature. Since these studies were for a climate location similar to Minnesota, the thickness of rigid insulation (R-value) could be proportionately reduced in milder climates."
In other words, you should be fine with 1/2 inch XPS. (You never mentioned which part of eastern Pennsylvania you're in.)
I certainly wouldn't leave those closets unfinished. It's like insulating, then leaving a door open. Just adhere the XPS where you can, then frame across and use the fg.
Besides XPS, you can also use EPS on basement walls. It has a lower initial R value, but is cheaper. But I would use at least 1" EPS that is not covered in foil.
The key to success with less XPS is using a dehumidifier during the summer months.
Now don't tell me this isn't in the budget either!
andrelaplume2
Original Author15 years agoHa! The only thing not in the budget is the XPS, celing and floor...just kidding.
To be honest there will be a whole portion of the basement not finished...just walled off. This is the storage area and portion where the bilko door is, my workbench etc etc. It is the area most likely to get flooded if that should occur. Also the area where the washer/dryer/sink is will not be finished...just doored off....too many pipes to get around. The closet would be very difficult as well...many pipes in there too. It is not the best layed out basement. I will likely go wit the 1/2 blue DOW styrofoam of 1" white, whichever I can find cheapest.
In the coldest of winter it seldom gets below 55 and is usually closer to 60 so this all can only help.
If they make something I can put over the concrete that does not require drywall over it, let me know...I can perhaps squeeze that between pipes and such in the unfinished basement portion.
Thanks!
Sorbet
15 years agoI am facing exactly the same conundrum as andre. last week I called a local radio station show Mr. fixit (wgn radio chicago)who said not to use the xps because it would trap moisture? Rather, he said to space the wall 1-2 inches from concrete foundation and use fiberglass batts with kraft facing interior of room. He also said to place vents between drywall and foundation wall to lets things breathe. I am really confused. Mr. fixit is also nationally renowned.
worthy
15 years agosaid not to use the xps because it would trap moisture
XPS tight to the wall raises the temperature of the wall so water vapour does not condense against the wall. That's in winter. In summer, the XPS abovegrade does not "trap" but instead impedes the movement of water vapour into the basement because it has low permeance; the vapour that does move through is then easily handled by mechanical dehumidification.
When "Mr. Fixit's" methods are published in leading building science journals, adopted and promoted by the US Department of Energy and Building Code writing officials, let us know. Where, btw, did he earn his Phd. in engineering?
You can search the many links I've provided to Dr. Lstiburek, Building Science Corp. and the US Department of Energy. Or you can follow Mr. Fixit's folklore.
P.S. I love Mr. Fixit's venting idea! It guarantees wet interior foundation walls in the winter and the free movement of water vapour into the basement during the summer. And the insulation serves no purpose as the thermal barrier is breached by the vents. Totally useless!
I don't want to sound superior. We've got our own H&G Mr. Fix-it who constantly talks about the importance of warm side poly vapour barriers in the basement, when he's not decrying the "shoddy workmanship" of others.
andrelaplume2
Original Author15 years agoJust what I needed to read! Personally I would find it hard to believe there would be mositure issues in that 2" space; especially with vents as well. Then again they ain't askin' me for rocket ship designs for a flight to Mars! I do wonder why; if mold/moisture is that prevalent, that code does not require XPS throughout the country? Of course gov beaurocrasy could be in play.
My hope is that the XPS I am using at worse turns out to be overkill..not lead to problems. I just want to eliminate potential mositure problems.
Now a question. I do NOT want to put the Wallmate type stuff up with the drywall right against it and have mold creeping thru. Ditto in the area where I am tapcon-ing 1/2 XPS up and framing up against that with 2X4s and batted kraft backed insulation. Buildng sciences seems to indicate there is no chance BUT I do keep hearing that the XPS needs to be tight against the concrete.
What is there definition of tight? I do not want to see any mold in a year or so and then get some technicality out of Bulding Sciences about tightness. My basement is poured concrete and smooth except for every 2 feet or so where there were likely forms. I end up with rough areas running vertically maybe 3/4 wide every 2 feet. Also, who knows how plumb the walls are. The 1.5" wallmate is rigid. If the concrete bows a bit, I doubt the XPS has enough give to 'touch' the concrete in every spot. The 1/2" XPS is likely more pliable but I bet there will be areas where it may bubble out from the wall too. There will likley be some space in and around those rough ridges too.
So was is the definition of tight? I can forsee areas where you likely could slide a sheet of paper between the Xps and concrete...maybe gaps up to 1/8"...more?
I just do not want to find out that the XPS only works on perfectly plumb smooth walls.
So before I start tapcon-ing..........
worthy
15 years agoBlock walls are perfectly suited to Wallmate or equivalent. The irregularities on a poured wall make it better suited to XPS or equivalent. The ridges (where concrete poured out between the forms during the pour, or forms weren't perfectly aligned) mean that on some boards you're going to have put more concrete screws than others to achieve a tighter fit. It will never be perfect. That's why you can tape the seams. Forget slipping in a piece of paper. This isn't trim carpentry work!
Framing over the XPS or equivalent gives you the opportunity to increase the R value of the wall. But don't leave a space. This only creates voids, which lead to air currents degrading the value of the insulation.
As I mentioned before, instead of XPS, you can use Membrain, a smart vapour retarder that changes permeability depending on the ambient humidity; it has performed well on University of Minnesota tests (see link). I have no experience with it, as it was only approved this year in Canada.
Here is a link that might be useful: Membrain
andrelaplume2
Original Author15 years agoI was not going to slip paper in there....just driving home the point that it likely will never be 100% tight and trying to determine what an acceptable tolerance would be...paper thin, 1/8 etc. Block construction will pretty much have a small indent around each block so I guess some space is ok.
Sorbet
15 years agoandre, i admire your enthusiasm about this topic. i sometimes wonder why there is such an obsession with keeping things so air tight. apart from the fact no system can guarantee a 100% against air infiltration or even if something comes close it would most likely be cost prohibitive, would it be desirable to have no air exchange in a basement? some air leakage may actually be good. also, below grade basement temperatures bottom out at 55-60f at least where i live, so how much money are we really saving for that ever elusive quest for r-value? please do not take this as a personal attack but i would like your insight.
andrelaplume2
Original Author15 years agoI was hoping the insulation would perhaps net a slightly warmer basement....my real concern was mold issues.
saxmaan1
15 years agoIn my opinion, this is all hoop la. Install your framing and install kraft faced insulation. You will be fine. It will also be approved by your code official. I tore apart many a basement and never found any trace of mold and water running down walls. Just not true.
Sorbet
15 years agoI have plenty of space in my basement so I will have contractor frame new wall a foot or so away from foundation wall. It will have a access panel or door at one end so I will be able to physically see what is going on behind the wall as times passes. I will most likely use fiberglass batts in this scenario. I would not hesitate to use xsp, but the cost of materials and labor and most importantly correct installation (since I have drain pipes along foundation wall which will require a lot of cutting of xsp) has me hedging against this idea.
Sorbet
15 years agoI have plenty of space in my basement so I will have contractor frame new wall a foot or so away from foundation wall. It will have a access panel or door at one end so I will be able to physically see what is going on behind the wall as times passes. I will most likely use fiberglass batts in this scenario. I would not hesitate to use xsp, but the cost of materials and labor and most importantly correct installation (since I have drain pipes along foundation wall which will require a lot of cutting of xsp) has me hedging against this idea.
andrelaplume2
Original Author15 years agoanyone know of any place you can get 3/4 X 4 X 8 sheets of XPS, HD only has 2 X 8s and Lowes only has 1/2 X 4 X 8...which I may just use...
worthy
15 years agoCall around to your local lumber yards. Not all sizes are available in all regions.
chpwaman
15 years agoYou could check a place like Craigs list for XPS. I saw an ad (not in your area) where a guy was selling 48 sheets of the 1". It's too bad the HD in your area is so expensive. Here is Michigan I can get 1" 4x8 pink XPS for $10 a sheet.
andrelaplume2
Original Author15 years agoYea...its 6.86 at HD for pink 3/4" 2X8 sheets. I think I am going to use the 4X8 1/2 stuff from Lowes...$11 a sheet.
In some areas where I do not need to frame (bottom of steps/inside closet...I may just use the 1.5" pink xps stuff preslotted for fur strips....it will go up quicker.
Other areas I will use the blue 1/2" dow stuff from Lowes and frame against it with fiber insulation.
Nag
2 years agolast modified: 2 years agoPlease help me to understand the science behind this scenario:
I have poured concreat basement wall for 1994 built in Notth East PA; (not sure if insulated from exterior below grade). Basement is dry all time under my ownership from last 4 years;
Question # 1, if i am correct, pourced concreat wall is like spounge. What direction remaining water & vapour travel, if XPS is firmly attached to the concreat wall (after 0.6 permission vapour enter the interior of the basement).
Question # 2 If this vapour travel above grade, do i need to do any other insulation or worried?
Thanks
Nag
worthy
2 years agolast modified: 2 years agoHere is Building Science Corp.'s latest publication on basement construction.
The vapour drive will always be to the interior. However, the low permeance of XPS (or equivalent insulation) and the lack of vapour sensitive or vapour trapping materials in the finished walls means there should be no problems from moisture. Bulk (liquid) water is another matter. And a de-humidifier is still essential.
Nag
2 years agoThanks Worthy for giving me this reference and confidence.
fyi, Eight months back I have purchased following Impermeable Foil Insulation - Prodex to hang on basement wall and insert into the cove joint connected with french drain along the peremeter of the basement wall as recommended by one contractor, but had big dout if this creates mold on my walls over time being impermeable. i want to get this correct to avoide mold problems in future.
worthy
2 years agolast modified: 2 years agoTheoretically, that should work, as it's in accord with Dr. Lstiburek's Building Science Corp.'s recommendations, below.
Source: Building Science Corp.
It's important that it be impermeable. Since it's not going under the slab, the material should be impermeably adhered over the cove joint.Nag
2 years agoThanks again Worthy for your contributions all across various topics.
I think there is no perfect answer to choos between above two options, but your experience/Knowledge will help me to make best possible decision to minize the mold on concreat walls; rest all i think i can manage.
Current State of basement wall:- Smalls cracks fixed professionaly.
- Light Mild Green Mold/Marks bottom of the basement wall were cleanded with concrobium liquid before drylock
- DryLock anti-mold applied on wall after cleaning two coated applied;
- French Drail and Sump working; expected to be working; mostly dead dry;
- Never had water in the basement; in last 4years under my ownership (built in 1994); don't see any water damage/repairs from before also.
I Need to decide this week and move forward between below two options; any final recommendation pls. I know no perfect answer with garantee.
Option #1 XPS nailed/glued to concreat walll and sealed; As building science Lstiburek said, all concreat walls will crack/leak sometime for sure.
Optin #2 imperable from basement wall from top seal to bottom into Cove Joint.( To do this, I need to remove the fome inserted in the cove joint Tuck the imperable insulation. Means earth gases / vapour has way to get upto the top of the concreat wall but offcource it is tightly sealed all around.
Thanksworthy
2 years agoYou say you already have an interior perimeter drain and you've never had water in the basement and don't see sighs of past water damage either.
You then said you have Prodex. Just glue or otherwise affix it to the existing wall. Seems straightforward.
Pics would help if I'm missing something.Nag
2 years agoSorry if my previous email is confusing.
I mean I have purchased Prodex (Impermeable Foil Insulation - Prodex) in hurry but did not unpack/used, as I got to know risk of mold increases if impermeable attaced to the cocreat wall.
Question/Request:Cross checking, as I am ok to spend again on XPS Riged Form, but want to be sure again that using Prodex (Impermeable on wall increases the risk of mold). and method of tucking bottom of the Prodex is into the cove joint. and seal might not address the mold risk.
**This is like throwing away 1200$ worth of Prodex material in new unopend box's;
Note:As per your fist reference provided, Building Science recommends to use XPS Riged Form 1inch semi-impermeable 1.1 perms.
Thanks again for all yoru support! this could be my last post on this topic; request your opinion.worthy
2 years agoAn interior perimeter drain is typically used with an impermeable drainage matt on the interior walls. So there's no harm in attaching an impermeable insulation, such as the Prodex, on top or through the matt.
A pic or two of your walls would help clarify what you're working with.Nag
2 years agoThanks. Request after view below photos and video, please advice me, if i can use this prodex or need to buy XPS riged fome 1inch
Prodex Technical Data @ https://www.insulation4less.com/insulation/prodex/10m-prodex-total-insulation.
Video @ https://youtu.be/QTUo9Sh2lu4Photos
Nag
2 years agoPlease advice if good to procced with prodex i have at home or should i buy xps riged fome and attach to walls?
worthy
2 years agolast modified: 2 years agoThe photos and your caption indicate there is no interior drainage membrane. Your caption says the concrete wall is coated in DryLok and Concrodium. And the two-inch+/- opening along the foundation wall is more indicative of a poorly filled floor-to-wall joint than an interior perimeter drain.
As well, the sump setup is exactly what homes have where exterior perimeter drains are not allowed to tie into municipal storm drains. (To check if it is a perimeter drain, pour water into that open gap shown in your video and see if it runs into the sump.)
In either case, the Prodex can't hurt. But it will provide virtually no R-Value. Reflective insulation works in hot attics such as pole barns and the like. In fact, that's exactly how Prodex comes up with the R-22 value.
In that case, follow Building Science Corp. guidelines for basement insulation in your area. Use moisture insensitive insulation, such as foam boards and/or spray foam. Also, be sure to insulate the rim joist area similarly--boards and/or foam spray.Nag
2 years agoThanks for the info; I am not looking prodex as insulation at this time when connected to wall; expect that to work as air, vapor and radon barrier without mold problems on material or wall by tucking it into the cove joint.
For insulation, i am planning to use Rockwool anyhow as i need R value 16+. XPS also give me only 4-5 R value max as i cannot go above 1inch board as per building science recommend 1.0 perm.
Below is my idea (Prodex + Steel Studs + Rockwool + drywall)worthy
2 years agoi cannot go above 1 inch board as per building science recommend 1.0 perm.
That's a minimum, not a maximum.
Practically speaking, many builders combine the more expensive XPS boards with a cheaper fibrous insulation to the interior. (See Martin Holloday here.)
I've used 1" XPS above and below grade with fibreglass to the interior as per the detail below of a current project.
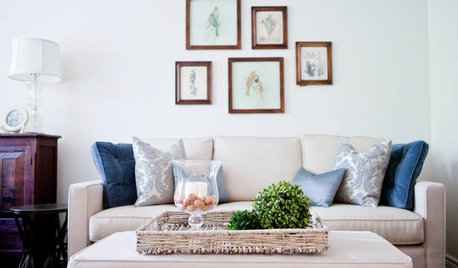
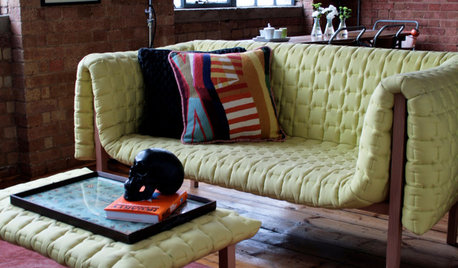
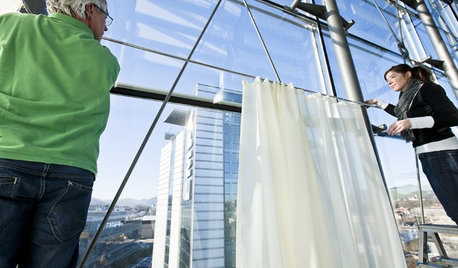
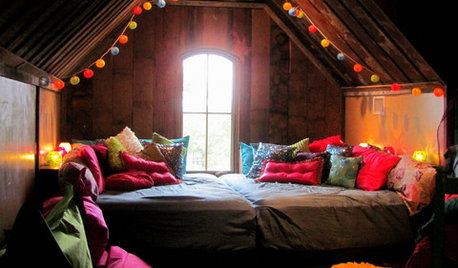
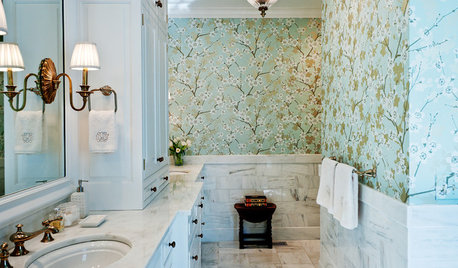
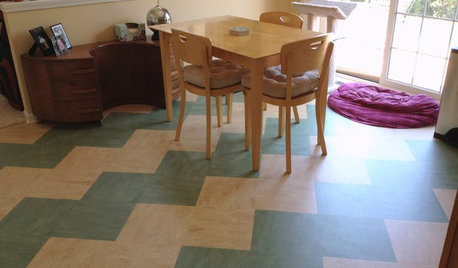
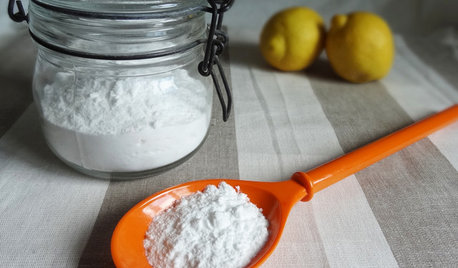
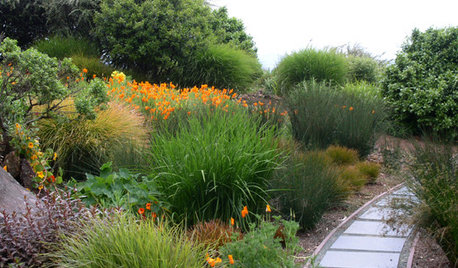
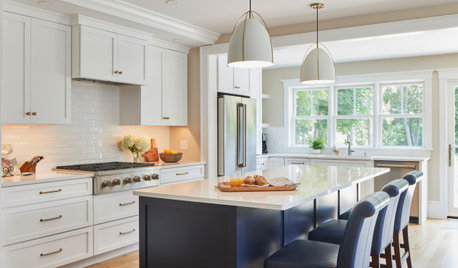
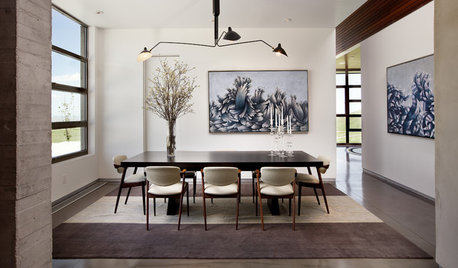
worthy