Basement with half wall--insulation questions
mohonri
12 years ago
Featured Answer
Sort by:Oldest
Comments (19)
worthy
12 years agomohonri
12 years agoRelated Professionals
Burlington General Contractors · Foothill Ranch General Contractors · Modesto General Contractors · Glens Falls Architects & Building Designers · Bothell Flooring Contractors · Chicago Flooring Contractors · Cottage Grove Flooring Contractors · Dublin Flooring Contractors · Mahwah Flooring Contractors · Panama City Beach Flooring Contractors · Parma Heights Flooring Contractors · Sarasota Flooring Contractors · Tewksbury Flooring Contractors · University Park Flooring Contractors · Princeton Meadows Basement Remodelingmohonri
12 years agoworthy
12 years agoDickRNH
12 years agoworthy
12 years agoDickRNH
12 years agoworthy
12 years agomohonri
12 years agoworthy
12 years agoDickRNH
12 years agomohonri
12 years agoworthy
12 years agomohonri
12 years agoworthy
12 years agomohonri
12 years agoworthy
12 years agomohonri
12 years ago
Related Stories
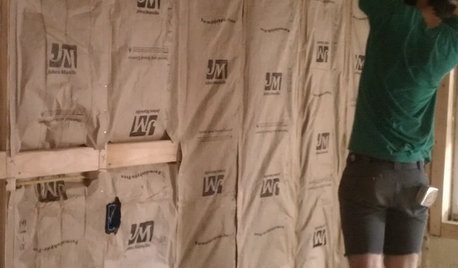
REMODELING GUIDESCool Your House (and Costs) With the Right Insulation
Insulation offers one of the best paybacks on your investment in your house. Here are some types to discuss with your contractor
Full Story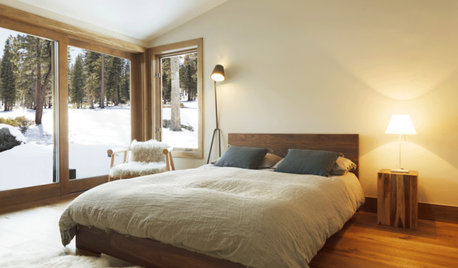
WINDOW TREATMENTSEasy Green: 9 Low-Cost Ways to Insulate Windows and Doors
Block drafts to boost both warmth and energy savings with these inexpensive but effective insulating strategies
Full Story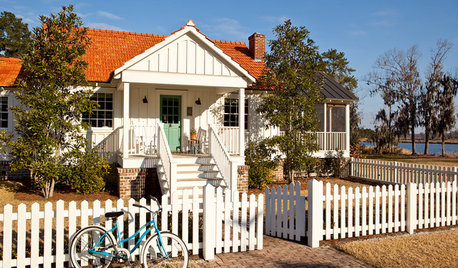
REMODELING GUIDESConsidering a Fixer-Upper? 15 Questions to Ask First
Learn about the hidden costs and treasures of older homes to avoid budget surprises and accidentally tossing valuable features
Full Story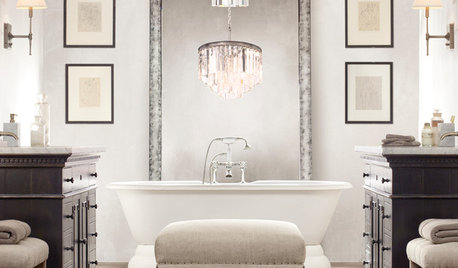
LIGHTING5 Questions to Ask for the Best Room Lighting
Get your overhead, task and accent lighting right for decorative beauty, less eyestrain and a focus exactly where you want
Full Story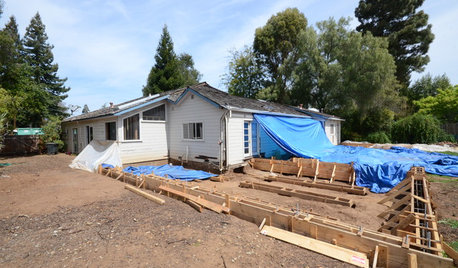
REMODELING GUIDESSurvive Your Home Remodel: 11 Must-Ask Questions
Plan ahead to keep minor hassles from turning into major headaches during an extensive renovation
Full Story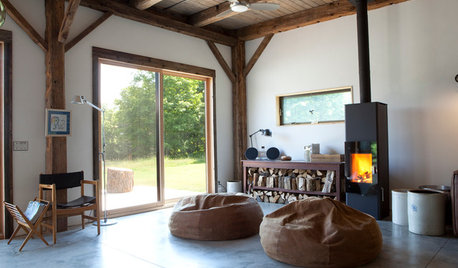
GREEN BUILDINGInsulation Basics: Heat, R-Value and the Building Envelope
Learn how heat moves through a home and the materials that can stop it, to make sure your insulation is as effective as you think
Full Story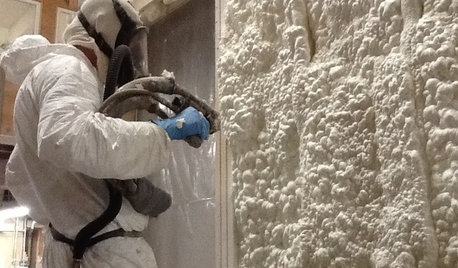
MATERIALSInsulation Basics: What to Know About Spray Foam
Learn what exactly spray foam is, the pros and cons of using it and why you shouldn’t mess around with installation
Full Story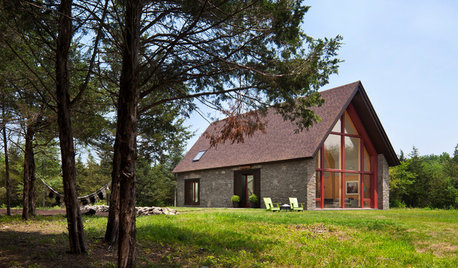
GREEN BUILDINGInsulation Basics: Designing for Temperature Extremes in Any Season
Stay comfy during unpredictable weather — and prevent unexpected bills — by efficiently insulating and shading your home
Full Story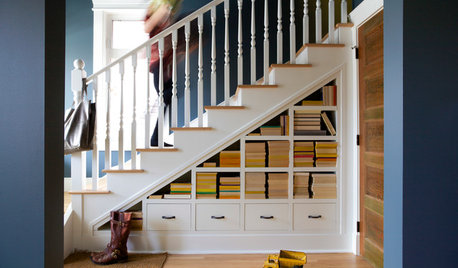
ORGANIZINGPre-Storage Checklist: 10 Questions to Ask Yourself Before You Store
Wait, stop. Do you really need to keep that item you’re about to put into storage?
Full Story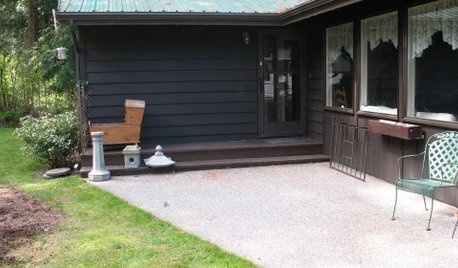
worthy